KUKA Next-Generation Mobile Robotics Come to MODEX 2024
KUKA Robotics will spotlight a pair of innovative mobile robots March 11-14 in booth B4003 at MODEX 2024 in Atlanta. The KUKA KMP 1500P autonomous mobile platform revolutionizes automation for intralogistic optimization. The KUKA KMP 600-S diffDrive mobile platform automated guided vehicle (AGV) advances industrial logistics with laser scanners and 3D object detection to meet the highest safety requirements.
KUKA Robotics will spotlight a pair of innovative mobile robots March 11-14 in booth B4003 at MODEX 2024 in Atlanta. The KUKA KMP 1500P autonomous mobile platform revolutionizes automation for intralogistic optimization. The KUKA KMP 600-S diffDrive mobile platform automated guided vehicle (AGV) advances industrial logistics with laser scanners and 3D object detection to meet the highest safety requirements.
The KMP 1500P autonomous mobile robot (AMR) makes an optimal contribution to intralogistic processes in production and storage facilities. With a 60 mm stroke and precision positioning, the AMR transports up to 1.5 tons of materials and workpieces, picks goods, supplies lines and cells with materials and transports production parts in process linking. The robot uses built-in technology and QR code readers to identify loads. It lifts all types of load carriers for easy implementation into existing industrial projects to optimize warehouse processes, streamline assembly lines and enhance complex material handling.
Differential drive, flexible mobility and the ability to adapt travel paths with autonomous efficiency enable this mobile platform to handle any dynamic, complex environment. To protect the KMP 1500P, its loads and the workplace, safety provisions include 3D cameras, laser scanners and IP class 54. The KMP 1500P charges both at a charging station and during work processes, with inductive, intelligent 24/7 charging management. KUKA's KMReS fleet manager greatly simplifies integration for the ideal combination of cost efficiency and safety. Maintenance is quick and easy, with replaceable control and switching electronics.
To transport demanding loads, the KUKA KMP 600-S diffDrive mobile platform automated guided vehicle (AGV) moves at speeds up to 2 meters per second in all directions of travel and offers up to 600 kg of payload capacity. An integrated lifting device lifts up to 60 mm in under 3 seconds. The vehicle requires no safety fencing, which provides maximum freedom of movement for employees.
When cycle times require high-speed travel, front and rear-mounted laser scanners ensure safe operation in all travel directions. Camera-based 3D object detection enables the KMP 600-S diffDrive to integrate seamlessly into existing production environments and detect obstacles autonomously from 50 mm up to 2.1 m above the ground. Ideally equipped for tough industrial environments, the KMP 600-S diffDrive features an IP 54 design that works reliably even in adverse conditions such as water spray and dust.
For optimal support of in-house material flows, applications for the KMP 600-S diffDrive program in Java and use initial teaching. A manual controller provides quick, easy commissioning. With quick firmware updates and tool-free access to components including rollers, laser scanners and service interfaces, the platform is easy to maintain, inspect, calibrate and repair.
KUKA
KUKA is a global automation corporation with sales of around 3.3 billion euro and roughly 14,000 employees. The company is headquartered in Augsburg, Germany. As one of the world's leading suppliers of intelligent automation solutions, KUKA offers customers everything they need from a single source: from robots and cells to fully automated systems and their networking in markets such as automotive, electronics, metal & plastic, consumer goods, e-commerce/retail and healthcare.
Featured Product
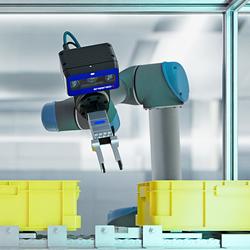