Robots equipped with AI vision systems, such as MIRAI, can perceive and adapt to their surroundings. This allows them to handle variance while performing complex tasks, making it possible to automate operations otherwise considered too complex to solve.
Five challenging applications automated with AI-powered robots
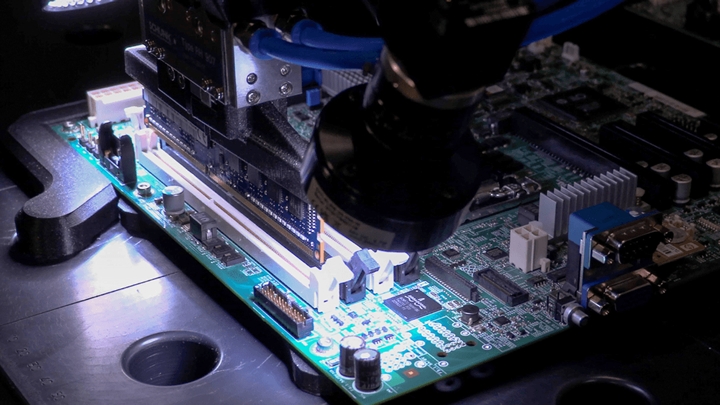
Article from | Micropsi
Industrial robots have revolutionized manufacturing by boosting productivity, efficiency, safety, and quality, all while cutting costs. They excel in repetitive tasks such as palletizing, welding, and assembly, they free up employees for more engaging tasks, and fill labor gaps. Despite their benefits, traditional robots need predictable settings. If scenarios deviate from what they have been programmed for – if variance occurs – human intervention is required.
The introduction of robotic vision systems powered by artificial intelligence marks a turning point in automation. Robots equipped with AI vision systems, such as MIRAI, can perceive and adapt to their surroundings. This allows them to handle variance while performing complex tasks, making it possible to automate operations otherwise considered too complex to solve. Join us as we explore five applications where AI-powered robots are redefining the limits of automation.
Leak testing of heating and cooling systems
Leak testing is a common task in the white goods and the automotive industry to detect and pinpoint leaks in heating and cooling systems. This ensures that products function properly and meet quality standards.
For leak testing of refrigerators, a so-called sniffer probe is run along the metal pipes and compressors of a fridge to check solder joints for leaking coolant. The challenge: The back of each refrigerator is unique in terms of position, color, shape, and even the amount of solder points. For a conventional robot, such variances are an insurmountable obstacle, which makes this task impossible to automate.
At their production site in Spain, BSH Hausgeräte demonstrates how leak testing can be automated. The European market leader for home appliances uses robots equipped with our vision system MIRAI to perform leak testing. Instead of programming the robot, BSH employees showed the MIRAI system the solder points during training using a camera attached to the robot arm. Based on a few training examples, the system generates appropriate responses to new situations during ongoing operation.
Thanks to MIRAI, robots at BSH today reliably identify all solder joints to be inspected and approach the sniffer probe with millimeter precision – regardless of position, shape or color of the joint. To achieve extreme robustness, the system can correct robot movements in real time. By automating leak testing with an AI-powered solution, BSH enhances quality and process consistency while lowering operating costs and reducing maintenance and troubleshooting needs.
Leak testing - A BSH employee shows the AI-powered MIRAI vision system the solder joints to be inspected during training.
End-of-line testing for electrical safety
Robots powered by AI vision-systems can also be deployed to automate other end-of-line tests. VDE testing, a standardized electrical safety process, verifies the safety and quality of electrical devices and components before they leave the factory. During this process, testing probes are commonly used to evaluate the product's functionality and safety. Like leak testing, the testing probe must be guided to specific points like the wires inside the device, to check for loose connections. It also needs to be applied to various components to measure voltage, current, and resistance.
Since these components, particularly wires, are not always positioned identically, their locations cannot be defined by fixed coordinates. AI vision-systems can be trained to identify the locations requiring inspection so that the probe can be guided accurately by the robot for testing.
Pick and place of randomly positioned metal parts
Pick and place is a common application in manufacturing. Variations of this task are often already automated. However, things get tricky when parts of the process are unpredictable, e.g. when the position or shape of a workpiece varies, or the workpiece being handled is flexible.
Family-run heat treatment company HWL Löttechnik GmbH identified a pick-and-place task at its production facility in Berlin, Germany, that would benefit from automation. The task constitutes two parts. In one, a shiny metal rod – lying among about 50 others – is picked from a basket. In part two, that rod is brought to and inserted upright onto a large, circular, horizontal-facing rack covered with pegs. During picking, the rods aren’t in predictable positions in the basket. During placing, the rack pegs aren’t in predictable positions. Conventional robot solutions failed due to this variance in position. Because the rods are made of metal, they produce reflections that standard vision systems struggle to interpret.
HWL turned to us to train a MIRAI-equipped cobot to automate this task, overcoming variance in position, form, lighting, and background. Since the AI-powered solution was implemented, HWL has managed to optimize cycle times by 20%. The AI vision system has helped the company reduce costs and relieve staff of tedious work.
Pick and place - A MIRAI-controlled robot handles reflective metal parts in a pick-and-place-task.
Insertion of DIMM modules
Dual inline memory modules (DIMMs) are a frequently used component in the manufacturing of electronic devices. They are used as RAM and are installed in slots on the mainboards of computers, servers, and other devices. Although DIMMs are ubiquitous, they are still often inserted manually in production, even though this task can quickly become painful for workers due to the modules' sharp edges. However, the modules and mainboard slots are extremely narrow and require precise and gentle handling to avoid damage during insertion. The position of the mainboards often varies, and they may move on conveyor belts. Positioning of the slots and coloring also vary from mainboard to mainboard – too many unpredictable circumstances for robots.
To automate this task for a server manufacturer, we collaborated with the Fraunhofer Institute for Factory Operation and Automation in Magdeburg, Germany. Our setup, featuring a FANUC LR 10 robot equipped with MIRAI, was able to handle the variance in position and color of the mainboard and slots and managed to achieve the cycle times and correct force values required by the customer.
Screwdriving despite position, part, and angle tolerance
Screwdriving assembly processes are common in all manufacturing industries. While screwdriving may appear simple, automating it can pose significant challenges. This stems from several types of variance that arise in production workstations involving screwdriving.
The location of screw holes can become unpredictable when variance occurs in the positioning of the parts within the workstation or when production tolerances cause variance in the parts themselves. Another major difficulty is variance in screw insertion angles caused by uncertain screw hole locations or unaligned screw holes. Together, these variances make reliable robotic automation of screwdriving extremely difficult.
To take up the challenge, we teamed up with DEPRAG, a producer of screwdriving systems. In a test case, we used our MIRAI vision system and DEPRAG’s screwdriving technology attached to a Universal Robots UR16e robot to drive four screws into an electronic module, joining the top piece to the base. In the process, the robot positions the screw (fed by the DEPRAG system) 50-60 mm from the screw hole. The MIRAI system takes control from the native robot controller and position the screw tip above the threaded hole. At this point, the DEPRAG system assumes control again, inserts and secures the screw to a specific torque value or angle position. Simultaneously, the screwdriver is fed the next screw. The native robot controller moves the robot to approach the next hole in the module.
With this setup, the system can handle variance in the position of the electronic modular in the workstation as well as variance in the angle at which to insert the screws into the holes. It can be set up and made ready for deployment in less than one day.
Screwdriving - AI-powered robots can handle different types of variance in screwdriving assembly processes.
AI's transformative role in manufacturing
The integration of AI-powered robotic vision systems such as MIRAI into manufacturing processes is an important factor in tackling complex manufacturing tasks. These systems provide adaptability in unpredictable environments and can handle different types of variance, allowing more processes to be automated – important in addressing ongoing labor shortages. Other crucial benefits are reduced costs, improved product quality, and increased productivity over time. In the future, AI-powered robots will play a central role meeting the increasing demands of a competitive market.
The content & opinions in this article are the author’s and do not necessarily represent the views of RoboticsTomorrow
Comments (0)
This post does not have any comments. Be the first to leave a comment below.
Featured Product
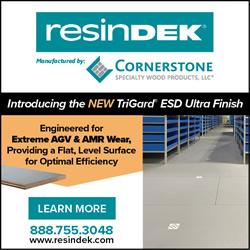