How Does a Fully Automatic Changeover Manifold System Work in Factory Automation Manufacturing?
Jewellok Design Ultra High Purity Gas Delivery System In Semiconductor Industry, Manufacturing Specialty Gas Changeover Manifold System, Ultra High Purity (UHP) Gas And Chemical Delivery Systems, Ultra High Purity Regulators, Ultra High Purity Diaphragm Valves, High Purity Regulators
How Does a Fully Automatic Changeover Manifold System Work in Factory Automation Manufacturing?
In the fast-paced world of modern manufacturing, efficiency, reliability, and uninterrupted operations are critical to success. A key element that supports these goals is the management of supply systems for gases and fluids, which are often vital to production processes. A fully automatic changeover manifold system is an advanced solution designed to ensure a continuous supply by seamlessly switching between sources—such as gas cylinders or fluid tanks—when one is depleted. This article explores how such a system operates within the context of factory automation manufacturing, shedding light on its components, functionality, and significance.
What is a Changeover Manifold System?
A changeover manifold system is a device that connects multiple supply sources to a single output line, typically used to manage the distribution of gases or fluids in industrial settings. In a fully automatic configuration, this system is equipped with sophisticated components that allow it to switch between sources without human intervention. The core purpose is to maintain a steady flow of materials to the manufacturing process, preventing disruptions that could halt production or compromise product quality.
Key Components
The system relies on several essential components:
1. Sensors: These devices monitor the status of the supply sources. For gas systems, pressure transducers measure the pressure inside a cylinder, signaling when it drops below a set threshold. For liquids, level sensors might track the remaining volume in a tank.
2. Automatic Valves: Typically solenoid-operated valves, these open or close based on electrical signals from the control system. In some cases, pneumatic valves are used in environments where electrical components are impractical.
3. Control System: A Programmable Logic Controller (PLC) or dedicated controller processes sensor data and manages the changeover process, ensuring a smooth transition between supply sources.
4. Manifold: The physical structure that connects multiple supply inputs to a single output, facilitating the flow of materials.
5. Alarms or Indicators: These alert operators to system events, such as a completed changeover or a supply issue, often via visual displays or audible signals.
How Does It Work?
The operation of a fully automatic changeover manifold system follows a systematic process to ensure uninterrupted supply. Here's a step-by-step breakdown:
1. Monitoring: Sensors continuously track the active supply source. For instance, in a gas system, a pressure sensor monitors the cylinder's pressure. If it falls below a predefined level—indicating the supply is nearly exhausted—the sensor activates.
2. Detection: The sensor sends a signal to the control system when the supply reaches a critical point.
3. Decision Making: The control system, such as a PLC, analyzes the signal and determines the next supply source to activate, often based on a preprogrammed sequence.
4. Valve Operation: The control system executes the changeover:
- Closes the valve of the depleted supply.
- Opens the valve of the next full supply.
This transition occurs rapidly—often within seconds—to maintain a consistent flow to the manufacturing process.
5. Notification: The system updates operators through alarms, status indicators on a control panel, or digital notifications, prompting them to replace the depleted source.
6. Logging: Data about the changeover, including timestamps and supply levels, may be recorded for analysis, aiding in maintenance and inventory management.
This automated process ensures that production continues without interruption, even as supply sources are exhausted.
Integration in Factory Automation
In factory automation, the changeover manifold system is not a standalone unit but part of a larger interconnected network. Its integration enhances its functionality and aligns it with broader production goals. Key aspects include:
- Centralized Monitoring: Through a Supervisory Control and Data Acquisition (SCADA) system, operators can oversee the manifold system alongside other plant operations from a single interface, tracking supply levels and changeover events in real-time.
- Data Collection: The system gathers data on usage patterns and changeover frequency, enabling predictive maintenance. This helps manufacturers anticipate supply needs and optimize inventory, reducing costs.
- Coordination: The system syncs with production demands, ensuring supply availability matches process requirements. It communicates using industrial protocols like Modbus, Profibus, or Ethernet/IP for seamless integration with other automated systems.
This connectivity transforms the manifold system into a vital cog in the factory automation ecosystem, enhancing overall efficiency and control.
Benefits
The adoption of a fully automatic changeover manifold system offers numerous advantages:
- Minimized Downtime: By preventing supply interruptions, the system keeps production lines running smoothly, boosting productivity.
- Enhanced Safety: Automation reduces manual handling of supply sources, minimizing human error and exposure to hazardous materials like toxic gases.
- Cost Savings: Efficient supply management cuts waste and prevents costly production stoppages, while data insights optimize inventory planning.
- Improved Quality: Consistent supply parameters—such as pressure or flow—ensure product quality remains stable, especially in sensitive manufacturing processes.
Applications
These systems find applications across diverse industries where continuous supply is critical:
- Pharmaceuticals: Nitrogen gas, used to prevent oxidation in drug production, is managed by changeover systems to maintain sterile conditions and product integrity.
- Food and Beverage: In packaging, nitrogen preserves freshness. The system ensures this gas is always available, avoiding delays or spoilage.
- Semiconductor Manufacturing: Ultra-pure gases are essential for chip fabrication. Any interruption risks significant losses, making automatic changeovers indispensable.
- Chemical Processing: For handling reactive or hazardous gases, the system provides a safe, reliable supply, reducing risks associated with manual intervention.
Considerations for Implementation
Implementing a fully automatic changeover manifold system requires careful planning:
- Sensor Selection: Choose sensors suited to the application—pressure sensors for gases, level sensors for liquids—ensuring accuracy and reliability.
- Compatibility: The system must integrate with existing automation infrastructure, including PLCs and SCADA networks.
- Redundancy: Build in failover mechanisms, such as backup sensors or controllers, to handle component failures without disrupting supply.
- Maintenance: Regular sensor calibration and system testing are essential to ensure consistent performance. Establish a maintenance schedule to prevent breakdowns.
- Training: Equip personnel with the knowledge to interpret system alerts and troubleshoot issues, maximizing its effectiveness.
Conclusion
A fully automatic changeover manifold system is a cornerstone of modern factory automation manufacturing. By automating the switch between supply sources, it guarantees uninterrupted operations, enhances safety, and drives efficiency. Its integration into automated networks, coupled with its wide-ranging benefits and applications, makes it an invaluable asset across industries. As manufacturing continues to evolve, such systems will remain essential in supporting the reliability and productivity demands of the future. With proper implementation and maintenance, they provide a robust solution for managing critical supplies, ensuring seamless production in an increasingly automated world.
Featured Product
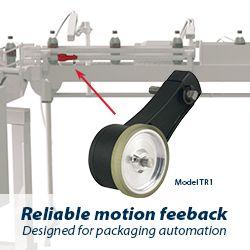
Model TR1 Tru-Trac
The Model TR1 Tru-Trac® linear measurement solution is a versatile option for tracking velocity, position, or distance over a wide variety of surfaces. An integrated encoder, measuring wheel, and spring-loaded torsion arm in one, compact unit, the Model TR1 is easy to install. The spring-loaded torsion arm offers adjustable torsion load, allowing the Model TR1 to be mounted in almost any orientation - even upside-down. The threaded shaft on the pivot axis is field reversible, providing mounting access from either side. With operating speeds up to 3000 feet per minute, a wide variety of configuration options - including multiple wheel material options - and a housing made from a durable, conductive composite material that minimizes static buildup, the Model TR1 Tru-Trac® is the ideal solution for countless applications.