JLS Automation Selects the ABB IRB 360 FlexPicker Delta Robot for its new Osprey System for Low Profile Case Packing
The Osprey is the first case packing system designed for installation in high sanitation areas; able to be placed at discharge point of primary packaging
JLS Automation has selected the ABB IRB 360 FlexPicker™ robot for its new Osprey case packing system, designed for loading low profile wrapped or vacuum packed product into shallow shipping cases. The Osprey is the first case packing system in the industry designed for installation in high sanitation areas of food packaging plants, and, along with an innovative compact footprint, is able to be placed at the discharge point of primary packaging systems. The low profile case configuration is common for many meat, poultry, seafood, cheese and frozen food products.
The ABB FlexPicker, the industrys first "second-generation" delta robot with over 4,500 global installations in the past 13 years, is uniquely suited for the Osprey case packing system. It is designed to enable easy cleaning and reduced maintenance, and is the only delta robot on the market available in washdown, stainless washdown and cleanroom versions with ratings as high as IP69K. It is available in a variety of configurations to meet payload, performance, working range and sanitation requirements. The smaller footprint enables valuable space to be kept to a minimum and allows it to be built into machines and productions lines for many packing applications.
"JLS has been integrating ABB robots for a number of years, including the FlexPicker. But until the IRB 360 was introduced with an IP69K rating we were hesitant to really aggressively pursue primary packaging applications in the meat, poultry, and cheese industry," said Craig Souser, president of JLS Automation. "Now we are leveraging our success with our Talon systems and offering the Osprey case packer, providing our clients a "one stop shop" for their primary and secondary packaging automation."
A vision inspection system allows the Osprey to track and handle randomly oriented and spaced products, and a vacuum leak detection system assures that only completely sealed packages are cased. Depending on the variables of individual primary packaging lines the Osprey can achieve throughput rates of 85 to 120 packages per minute. The Osprey can also be supplied with an integrated case erector and top and bottom case sealer.
"We are excited to be working with JLS on their new Osprey case packing system and salute their innovation and long history as one of our most valued and trusted partners," said Joe Campbell, vice president of the ABB Robot Products Group in the US. "This is another example of their leadership in applying the superior performance and versatility of the FlexPicker to a wide range of applications."
JLS has developed the Osprey in a modular format making the delivery faster than many traditional case packing systems.
About JLS Automation
JLS Automation, based in York, PA, is a leading supplier of packaging systems for the food industry, including high speed picking and product feeding systems. JLS is a member of PMMI and FPSA.
About ABB
ABB is a leader in power and automation technologies that enable utility and industry customers to improve their performance while lowering environmental impact. The ABB Group of companies operates in around 100 countries and employs about 124,000 people.
About ABB Robotics
ABB Robotics is a leading supplier of industrial robots - also providing robot software, peripheral equipment, modular manufacturing cells and service for tasks such as welding, handling, assembly, painting and finishing, picking, packing, palletizing and machine tending. Key markets include automotive, plastics, metal fabrication, foundry, electronics, machine tools, pharmaceutical and food and beverage industries. A strong solutions focus helps manufacturers improve productivity, product quality and worker safety. ABB has installed more than 190,000 robots worldwide.
Featured Product
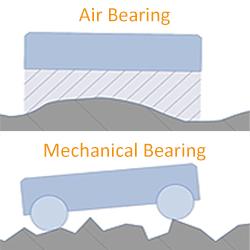