FANUC Robotics Demonstrates M-3iA Intelligent, Flexible, and High-Speed Delta Robot at Automate 2011
FANUC Robotics America will demonstrate its latest M-3iA intelligent, parallel-link robot designed to maximize speed and flexibility for assembly, small part handling and picking applications at Automate 2011, held March 21-24, at McCormick Place, Chicago, booth #648.
ROCHESTER HILLS, Mich., March 21, 2011 - FANUC Robotics America will demonstrate its latest M-3iA intelligent, parallel-link robot designed to maximize speed and flexibility for assembly, small part handling and picking applications at Automate 2011, held March 21-24, at McCormick Place, Chicago, booth #648. The M-3iA robot is a larger version of the companys M-1iA delta-style robot. Available in a four- or six-axis model, the M-3iA offers the same unique parallel-link structure, and accommodates payloads up to 6kg. In addition, it has the largest work envelope of any robot in its class (1350mm x 500mm). At the show, the M-3iA/6A six-axis robot uses iRVision® Visual Tracking to locate randomly-oriented cookies on a moving infeed conveyor, then pick and place the cookies at 90 degree angles. Once the magazine is full, the cookies are emptied and the cycle repeats. Also at the show, an M-3iA/6S four-axis robot equipped with iRVision Visual Tracking picks randomly-placed plastic parts from an infeed conveyor. The robot orients the products and places them onto an outfeed conveyor. The demonstration features the M- 3iAs speed and visual tracking. "In an effort to minimize waste, product designers must determine how a product looks best and that means that the robot must be able to pick up a product that sits flat and put it down either at an angle or standing straight up," said David Bruce, product manager, FANUC Robotics America. "Our latest M-3iA/6A robot has the flexibility and accuracy to perform coin stacking and other applications in the food industry that have traditionally been handled by manual operators." The M-3iA six-axis model has a three-axis, patent-pending wrist for complex assembly tasks. The extreme flexibility offered by the three-axis wrist enables the robot to pick up and insert parts at simple or compound angles, and twist parts into place, similar to the flexibility offered by a manual operator. "The M-3iAs unique design makes it possible to automate the assembly of a variety of applications that could not be done with traditional SCARA-type robots," added Bruce. "We refer to our series of parallel-link robots as fists because they provide the accuracy and flexibility of a human hand." A four-axis M-3iA has a single-axis wrist for simple assembly and high-speed picking operations, offering speeds up to 4000 degrees per second. In addition, a hollow wrist allows hoses and cables to be routed internally, which minimizes wear and tear on the tooling cables. "The M-3iA is ideal for both simple and complex assembly of electronics, medical devices, pharmaceuticals, cosmetics, office supplies, consumer products, and solar panels," said Bruce. "A completely enclosed structure also makes it safe for food environments."
The M-3iA, like all FANUC robots, operates with the companys latest R-30iA controller with integrated intelligent functions such as iRVision ® , Force Sensing, Robot Link, and Collision Guard. The M-3iA robot offers a wide range of benefits, including:
• Patent-pending three-axis, parallel-link wrist maximizes flexibility.
• Portable and compact size allows operation in small spaces.
• Six-axis design (three-axis wrist) enables part feeding from the sides of a work zone, increasing the useable workspace.
• Four-axis design (single-axis wrist) moves parts at extremely high speeds; a hollow wrist allows tooling cables to be routed internally, minimizing wear and tear.
• Food option with food-grade grease features a special coating to handle acid and alkaline disinfectants, and low-pressure rinsing.
• Ability to work with primary (unpackaged) or secondary (packaged) food products.
• IP67 rating for the entire robot means the robot is waterproof and can withstand harsh environments, including dust and oil mist.
• Collision Guard detects robot collisions with external objects, minimizing damage to the part and robot.
• Robot Link controls and coordinates up to ten robots through a network exchange of robot positional data.
• FANUC Force Sensor is available for intricate assembly applications.
FANUC iRVision
FANUCs iRVision is a truly integrated, plug-and-go vision system that runs on the standard CPU of every FANUC R-30iA controller without any additional hardware. A single source solution developed and supported by FANUC, iRVision offers easy setup and operation for factory environments requiring 2D and 3D guidance, error proofing, visual tracking, and quality control - all with FANUCs world-renowned reliability.
FANUC Robotics America designs, engineers and manufactures industrial robots and robotic systems for a wide range of applications including arc and spot welding, material handling (machine tending, picking, packing, palletizing), material removal, assembly, paint finishing and dispensing. The company also provides application-specific software, controls, vision products, and complete support services. After 29 years of success, FANUC Robotics maintains its position as the leading robotics company in the Americas. A subsidiary of FANUC Corporation in Japan, the company is headquartered in Detroit, and has facilities in Chicago; Los Angeles; Charlotte; Cincinnati; Toronto; Aguascalientes, Mexico; and Sao Paulo, Brazil. Over 100,000 FANUC robots are installed in the Americas, and 220,000 worldwide. Contact FANUC Robotics at www.fanucrobotics.com or by calling 1-800-iQ-ROBOT, option 5. Also visit us on YouTube, Facebook and Twitter.
Featured Product
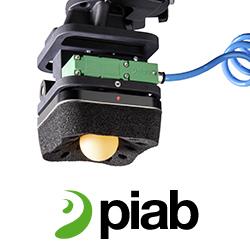