DE-STA-CO's CAMCO® Rite-Link Conveyor Delivers High Speed Precision in a Compact Design
Energy efficient link system is more stable and accurate than roller chain
Auburn Hills, Mich., July 15, 2011 - DE-STA-CO, a worldwide leader in robotic tooling, workholding and flexible industrial automation solutions, announces the release of a new product: the CAMCO® Rite-Link conveyor.
The energy efficient Rite-Link requires no lubrication, so it is virtually maintenance free. Built with lightweight components, it runs quietly, even at higher operating speeds.
"Rite-Link is the perfect fit for manufacturers that have been looking for a cost-effective conveying solution that is more accurate and stable than roller chain," said Lou Wozniak, Product Manager for DE-STA-CO. "Its easy to install and integrate into any shop environment, and lends itself to flexible indexing with CAMCO®s precision 115RSD rotary servo drive, or a customers standard servo and planetary drive."
About DE-STA-CO
DE-STA-CO is a global automation and workholding company, providing productivity solutions for the industry since 1915. Quality, innovation, and service have made DE-STA-CO a leader in the design and manufacture of cost reducing, flexible automation solutions for industrial customers around the world.
The company is committed to the Team DE-STA-CO philosophy, a progressive approach to doing business that focuses on providing consistent, standard-setting service and products to every customer, regardless of geographic location.
Featured Product
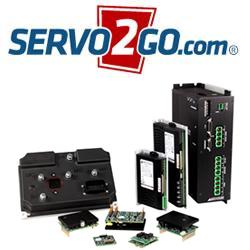
High Performance Servo Drives for localized and distributed control applications from Servo2Go.com
Engineered to drive brushless and brush servomotors in torque, velocity or position mode, Servo2Go.com offers a broad selection of servo drives in a wide range of input voltages and output power levels.