Multi-Axis Joint Modules suit lightweight applications.
Igus' "robolink" successfully tested in 100 beta applications
Robolink multi-axis joint modules from igus® are now available for order. Robolink is used for humanoid robots and other lightweight automation applications and includes a variety of options and components. These range from high-strength Bowden cables, to drive units and attachment accessories for the robot arm.
More than 100 beta-testers used free prototypes to further the development of robolink for a variety of applications before mass production began. The applications were diverse and ranged from underwater, mobile and humanoid robots, to dental technology and camera guidance for production monitoring and sewage-pipe inspection.
Design
Robolink joints combine design freedom with simplicity. To keep the dynamic forces of the system as low as possible, the actuators and control module are decoupled from the tools (e.g. grippers, hands or suction cups). The lightweight, maintenance-free, and corrosion-resistant joints are made from tribologically optimized plastics. They are driven by cables and can rotate and swivel freely. The lightweight feature and central drive option are important in the field of low-cost robotics.
Bowden cables used in the robolink system lower friction due to an optimized friction couple. A full range of mechanical accessories for attaching the robot joints and routing the Bowden cables includes flange shaft blocks, interior separators to divide drive and data cables, a cable tensioning system, and a range of cable pulleys.
Space-saving drive units featuring four drive motors and one housing, including cable deflectors and guides, are also available for the robolink system. The units use a configurable drive disc, which connects to the system. Users can attach the disc drive to a variety of different motor or gear shafts and then connect the wear-resistant cables.
Most recently, robolink was awarded the iF product design award 2011, which is internationally recognized as a marker for good design.
About igus
igus develops industry-leading energy chain® cable carriers, chainflex® continuous-flex cables, iglide® plastic plain bearings, igubal® spherical bearings, and drylin® linear bearings and guide systems. These seemingly unrelated products are linked together through a belief in making functionally advanced, yet affordable plastic components and assemblies. With plastic bearing experience since 1964, cable carrier experience since 1971 and continuous-flex cable since 1989, igus provides the right solution from over 80,000 products available from stock. No minimum order required. For more information, contact igus at (800) 521-2747 or visit www.igus.com.
Featured Product
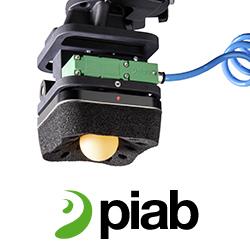
The piCOBOT Electric vacuum generator
Fully electric, slim design and absence of air-tubing and cabling. The new piCOBOT® Electric heads towards another success for Piab's piCOBOT® program. A secondary effect of these achievements is the absence of entangling air tubing and cabling. It simplifies the installation, and as the new piCOBOT® Electric only needs a single connection on the cobot arm, the clean set-up allows a completely unrestricted movement. The new piCOBOT® Electric package will contain plug & play software to fit UR e-series cobots, but many other useful adaptations will be introduced in the coming year