Toyota Assigned Patent for Movable Robot
Toyota, Toyota-Shi, Aichi-Ken, Japan, has been assigned a patent (8,010,232) developed by Yuichiro Nakajima, Toyota, Japan, Haeyeon Lee, Toyota, South Korea, and Hideki Nomura, Nagoya, Japan, for a movable robot.
Toyota, Toyota-Shi, Aichi-Ken, Japan, has been assigned a patent (8,010,232) developed by Yuichiro Nakajima, Toyota, Japan, Haeyeon Lee, Toyota, South Korea, and Hideki Nomura, Nagoya, Japan, for a movable robot.
The abstract of the patent published by the U.S. Patent and Trademark Office states: "A technique to wholly recognize the surrounding environment may be provided by excluding unknown environment which arises due to parts of a body of a robot hindering the sight of the robot during operations. The robot of the present invention is provided with a body trunk including head and torso, at least one connected member that is connected to the body trunk by a joint in which a driving mechanism is provided, a body trunk side camera that is arranged on the body trunk, and a connected member side camera that is arranged on the connected member. Further, the robot is provided with a composite image creation unit that creates composite image of a body trunk side image taken by the body trunk side camera and a connected member side image taken by the connected member side camera, such that a part of the body trunk side image is replaced with a part of the connected member side image so as to exclude the connected member from the body trunk side image."
The patent application was filed on Feb. 15, 2007 (12/279,561). The full-text of the patent can be found at http://patft.uspto.gov/netacgi/nph-Parser?Sect1=PTO2&Sect2=HITOFF&p=1&u=%2Fnetahtml%2FPTO%2Fsearch-bool.html&r=1&f=G&l=50&co1=AND&d=PTXT&s1=8,010,232&OS=8,010,232&RS=8,010,232
Featured Product
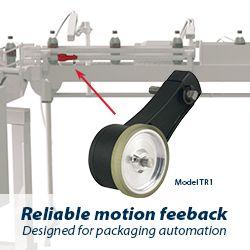
Model TR1 Tru-Trac
The Model TR1 Tru-Trac® linear measurement solution is a versatile option for tracking velocity, position, or distance over a wide variety of surfaces. An integrated encoder, measuring wheel, and spring-loaded torsion arm in one, compact unit, the Model TR1 is easy to install. The spring-loaded torsion arm offers adjustable torsion load, allowing the Model TR1 to be mounted in almost any orientation - even upside-down. The threaded shaft on the pivot axis is field reversible, providing mounting access from either side. With operating speeds up to 3000 feet per minute, a wide variety of configuration options - including multiple wheel material options - and a housing made from a durable, conductive composite material that minimizes static buildup, the Model TR1 Tru-Trac® is the ideal solution for countless applications.