Motoman Robotics and Universal Robotics Introduce New 3D Vision Solution for Box Moving Applications
Used in box moving applications, MotoSight 3D Spatial Vision locates randomly positioned boxes ranging in size from 6 to 48 inches at rates up to 12 boxes per minute.
Used in box moving applications, MotoSight 3D Spatial Vision locates randomly positioned boxes ranging in size from 6 to 48 inches at rates up to 12 boxes per minute. Using Logitech 9000 webcams and a Microsoft Kinect structured light sensor, the system locates boxes on pallets up to 48" square and as high as 60 inches. GigE cameras, improved optics, and more advanced structured light sensors can be used when higher accuracy is needed.
"MotoSight 3D Spatial Vision for box moving and depalletizing applications has
the potential to revolutionize how companies perform material handling operations in these areas," said Roger Christian, Vice President Marketing and Development at Motoman Robotics. "Powered by Universal Robotics' Spatial Vision Robotics software, we now offer 3D vision guidance solutions at 2D vision prices."
"MotoSight 3D Spatial Vision features Universal Robotics' 3D sensor and software technology, which enables Motoman robots to move any box in various orientations with arbitrary locations", said David Peters, CEO Universal Robotics. This is the first of a series of product releases that bring Spatial Intelligence to flexible automation, and is applicable for box moving, depalletization, and automated kitting solutions."
About Motoman Robotics
Founded in 1989, the Motoman Robotics Division of Yaskawa America, Inc. is a leading robotics company in the Americas. With over 230,000 Motoman robots installed globally, Yaskawa provides automation products and solutions for virtually every industry and robotic application; including arc welding, assembly, coating, dispensing, material handling, material cutting, material removal, packaging, palletizing and spot welding.
About Universal Robotics
Universal Robotics creates software that enables machines to learn from their experiences, react and adapt to their surroundings, and perform tasks that are costly, dangerous or difficult for humans to undertake. The company's signature technology, Neocortex™, which was developed over seven years at NASA and Vanderbilt University, will increase efficiency and worker safety across industries in applications including warehousing, mining, handling hazardous waste and automating vehicles such as forklifts.
Featured Product
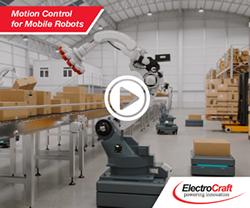