Self-Propelled Transporter Slashes Turbine Manufacturing Costs
Solar Turbine's Mabank TX manufacturing facility has incorporated a pair of Wheelift IP-SPMTs (In-Plant Self-Propelled Modular Transporters) into their manufacturing process to benefit from increased efficiency, effectively reducing the cost of manufacturing via the savings in time and personnel gained through the use of Wheelift's transporter technology.
Gas turbine engines, gas compressors, gas turbine-powered compressor sets, mechanical-drive packages and generator sets ranging up to 22 megawatts and 30,0000 horsepower can weigh as much as 150,000-200,000 lbs and the final packaged units are approx 30' long x 18'wide x 15' high. Moving the turbines and compressors through the manufacturing process can often be challenging, expensive and time consuming. Extra-heavy duty forklifts, contracted outside riggers and stationary, single purpose cranes have been the traditional methods used to move these behemoths from milling to assembly to shipping. Space constraints within the facility often restrict the ability to adopt the most efficient means during the manufacturing process when the products need to be maneuvered from one process to the next and finally packaged and prepared for shipping.
Headquartered in San Diego California, Solar Turbines Incorporated, a subsidiary of Caterpillar Inc is one of the world's leading manufacturers of industrial gas turbines. Following their San Diego plant's lead, Solar Turbine's Mabank TX manufacturing facility has incorporated a pair of Wheelift IP-SPMTs (In-Plant Self-Propelled Modular Transporters) into their manufacturing process to benefit from increased efficiency, effectively reducing the cost of manufacturing via the savings in time and personnel gained through the use of Wheelift's transporter technology. Stephen Burkhalter, Solar Turbine's Job Coordinator notes that use of Wheelift IP-SPMT allows Solar to operate 4 times more quickly and use 1/3 the personnel formerly needed. In addition to manufacturing efficiency, Solar avoided costly investments in real estate due to the maneuverability and precise movement capability afforded them by the Wheelift IP-SPMT (IN PLANT- Self Propelled Modular Transporters). "We purchased the transporters due to factory constraints. We don't have the space for big tugs. Our space is limited and, instead of spending the money on a new building or increasing our floor space these transporters, can turn very sharply and maneuver these packages in any way we choose." noted Paul Keifer, Solar Turbine's Value Stream Manager.
Wheelift IP-SPMT units enable new manufacturing and assembly line capabilities for in plant applications. The open-center axle concept allows designs that are compact with lower deck heights, yet with considerably heavier load carrying capacity per axle, while providing 100% equalized loading to every tire regardless of surface irregularities. With solid urethane tire assemblies, they are far more suitable for heavy moving systems across deteriorated floor conditions found in many heavy assembly and process applications. Low deck height, omni-directional steering, on-center rotation axle assemblies and all-wheel electric motor drives enable the transporters to maneuver in tight areas, make 90 degree turns, move diagonally, sideways, turn about any axis and precisely locate the product within thousands of an inch. The transporters are self propelled and self contained with a choice of LP gas, diesel or battery operation. There is a built in lift function to allow the unit to drive under, lift and carry any stand supported loads. Solar Turbine's application required the use of tandem operating transporters. The Wheelift system allows tandem operation by two four or more units.
Wheelift's Uniload wheel assemblies can also be built into the bases of heavy precision tooling fixtures and scaffolding structures where the Wheelift fluid suspension completely isolates the moving tools from undulations and other irregularities in plant floor surfaces. Massive structures can move in any direction with no resistance to reversing direction, essentially emulating precision ground rail movement. Wheelift's heavy load capabilities are applicable to virtually any process that requires moving heavy loads in tightly congested areas and spaces that have inadequate headroom or no capacity for crane coverage. Wheelift's New Designs Manager, Mel Terry offers, "Our customers are achieving significant gains in overall productively and an unheard of short return on investment. This new technology dramatically changes how manufacturers utilize their facilities by easily transporting and maneuvering huge assemblies, anywhere in plant on any floor surface. The ability to effortlessly maneuver in narrow and confined spaces, as well as transporting loads weighing 50 tons and greater between assembly areas and outside storage, completely changes how plant space can be utilized."
The Wheelift heavy transporter and trailer capability group is part of the Doerfer Companies' TDS Automation group, headquartered in Waverly, IA. Doerfer's proprietary Wheelift technology offers customers individual powered and controlled wheel modules that provide flexibility not previously available in moving very large payloads. Wheelift technology is currently employed in ship building, large plastic injection molding die changers, nuclear spent fuel storage transporters, and gas turbine manufacturing among other industries. In addition to its line of omni-directional transporters Wheelift manufactures self-propelled trailers utilizing two on center rotation electronically steered and driven independent axle assemblies with two AC servo-driven independently operated wheels. At the rear are two fixed direction rocker beam mounted axle assemblies with lateral articulation. This configuration allows for new levels of maneuverability including on center rotation around the center point of the rear axles. Doerfer was founded in 1961 to provide assembly automation and engineering services to the agricultural and metalworking industries. It has since grown to become the leading entity providing turnkey factory automation, press technology, tooling and automated guided vehicle technologies. These core competencies, applied to a diverse industry cross section, incorporate numerous advanced technological capabilities, including specialized expertise in the medical, nuclear, specialty fibers and chemical industries.
Featured Product
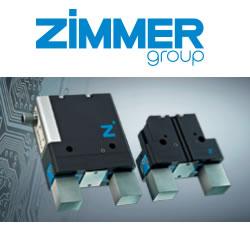