ABB to automate chemical complex in Saudi Arabia
ABB won the Main Automation contract for Sadara Chemical Company (Sadara), a joint venture between affiliates of Saudi Arabian Oil Company (Saudi Aramco) and The Dow Chemical Company (Dow).
Work is underway on establishing Sadara and the related integrated chemical complex in Jubail Industrial City, Saudi Arabia. When fully operational in 2015, the facility will be the largest plastics and chemicals production complex ever built in a single phase. All parties have agreed not to disclose the amount of the order.
ABB was selected as the project\'s Main Automation Contractor (MAC). The scope of supply includes process automation systems, safety systems, project management, project engineering, commissioning assistance, post-commissioning site support, as well as engineering, operator, and maintenance technician training.
"ABB\'s combination of leading-edge technology and extensive global and regional resources help it consistently execute large, complex projects like this one, so that our customers can operate successfully from the outset," said Veli-Matti Reinikkala, head of ABB's Process Automation Division. "Our competitiveness, long-term customer relationships and commitment to providing solutions achieving the highest levels of safety and efficiency were key factors in winning this order."
Saudi Aramco is a leader in oil exploration, production, refining, distribution, shipping, marketing and petrochemical manufacturing. Owned by the Saudi Arabian Government, it manages the world\'s largest proven oil reserves (260 billion barrels, nearly one quarter of the world's total), and the world\'s fourth-largest gas reserves.
Dow is a leading science and technology company and the foremost supplier of specialty chemicals, advanced materials, agrosciences and plastics. Dow manufactures more than 5,000 products at 188 sites in 35 countries across the globe, and employs about 50,000 people.
ABB is a leader in power and automation technologies that enable utility and industry customers to improve performance while lowering environmental impact. The ABB Group of companies operates in around 100 countries and employs about 130,000 people.
Featured Product
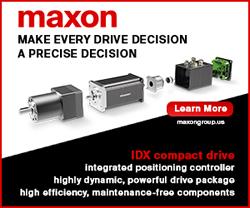
The maxon IDX Compact Drive with Integrated Positioning Controller
The compact brushless EC-i motor combined with an EPOS4 positioning controller delivers a highly dynamic, powerful drive package with field-oriented control (FOC), high efficiency, and maintenance-free components in a high-quality industrial housing. The maxon IDX drives are suitable for use across the entire speed range (from standstill to maximum speed) and have an extremely high overload capability. Together with a positioning controller, the integrated sensor (single turn) enables absolute positioning.