Portescap Introduces LVD Low-Voltage Servo Drive
Portescap introduces LVD Low-Voltage Servo Drive for small and large brushed DC or brushless motors.
Portescap introduces LVD Low-Voltage Servo Drive for small and large brushed DC or brushless motors. Packed in a high power-density package, LVD is powered from a supply voltage of 12-48VDC, and is capable of 7Amps RMS continuous and 12Amps RMS peak current with CANopen communication interface.
LVD offers extensive functionality with multiple I/O inputs and can be operated in Current, Velocity or Position modes. The drive operates at a voltage range of 12V to 48V and supports both BLDC and DC motors. Thanks to its selectable switching frequency, it also supports low inductance motors, making it an ideal drive for a wide variety of applications including surveillance cameras, semiconductor wafer handling processes, highly-sensitive medical applications and more.
LVD offers performance and accuracy thanks to its space vector modulation current loop and highly flexible tuning capabilities. In addition, LVD offers high sampling rates for the Velocity and Position loops, allowing wider bandwidth and increased accuracy.
Measuring only 117 x 83.5 x 21.5mm and weighing only 250g, the LVD is one of the smallest low-voltage drives. However, its small scale does not represent the power versatility that it can offer. With 12Amps RMS peak current and switching frequency of up to 100 KHz, LVD is also one of the most powerful low voltage drives in the industry, offering space efficiencies without compromising on performance.
Seamless configuration with Axis Manager- LVD's Axis Manager is an easy to use drive commissioning software. It features user friendly windows for motor and feedback configuration, various control loops tuning, I/O setup window, and comprehensive monitoring and recording features. The software communicates with the drive via RS232 or CANopen.
Featured Product
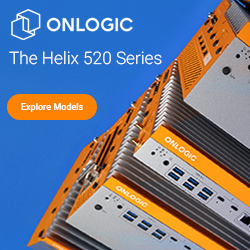
OnLogic's Helix 520 Series of Scalable Fanless Computers
The Helix 520 series utilizes the latest Intel Core Ultra processors with integrated edge AI capabilities to deliver exceptional performance and industrial-grade reliability for demanding applications in automation, robotics, machine vision, and more. Its unique modular design allows for flexible scaling of CPU and GPU performance, while robust connectivity and expansion options ensure seamless integration.