Pick and Place Unit offers less than 0.01 mm repeat accuracy.
Able to carry out high-speed assembly tasks with precision, freely programmable PPU-E30 is designed for vertical stroke of up to 100 mm, horizontal stroke of 270 mm, and moving mass of 3 kg.
Able to carry out high-speed assembly tasks with precision, freely programmable PPU-E30 is designed for vertical stroke of up to 100 mm, horizontal stroke of 270 mm, and moving mass of 3 kg. Cycle time is 0.58 sec, including switching and gripping times at 40 mm vertical stroke, 120 mm horizontal stroke, and moving mass of 2 kg. All utility lines for power supply, sensor, and pneumatic systems are plugged into rearward stationary connection, eliminating cable breaks and disturbances.
The fastest Pick & Place Unit on the market does not require any sensitive moving motor cables. With racing cycle times and an excellent repeat accuracy of less than 0.01 mm, it is setting benchmarks in the assembly of small components.
The PPU-E30 carries out high speed assembly tasks with the highest precision. Cycle time is only 0.58 seconds including switching and gripping times at a 40 mm vertical stroke, a 120 mm horizontal stroke, and a moving mass of 2 kg. All the utility lines for power supply, sensor, and pneumatic systems are plugged into the rearward stationary connection. Cable breaks and disturbances of the unit are now a thing of the past. The freely programmable unit is designed for a vertical stroke of up to 100 mm, a horizontal stroke of 270 mm, and a moving mass of 3 kg.
The narrow housing as well as the media supply via the back panel, allow a compact, maintenance- and assembly-friendly sandwich construction of several units next to each other. Two integrated linear encoder systems control the vertical and horizontal motion and assure a high repeat accuracy. Intelligent regulators control the cantilever arm as well as the actuators without a higher-ranking control unit. The required software is already integrated, thus the unit can be commissioned by simple Plug & Play.
Up to six integrated valves operated by one single air feeding, supplies all the pneumatic actuators. This minimizes the compressed air and consequently the energy consumption, and provides an enormous clock frequency. Since no motor or cables are moved, and the remaining moving components are manufactured in a light-weight design, the unit proves to be energy-efficient and economic. It works together with the SCHUNK module program and can be equipped with various actuators. In the largest construction stage, the PPU-E30 can utilize an electric rotary module with rotary feed-through, but also with two sensors and pneumatic connections.
Featured Product
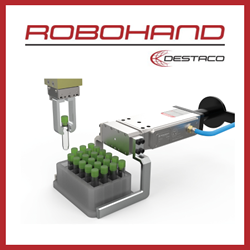