Miyachi Unitek to Showcase Laser Marking and Resistance Technology at Medical Design & Manufacturing (MD&M) West
Demonstrations and displays of medical marking, micro welding, and cutting capabilities
MONROVIA, CA - Miyachi Unitek Corporation, a leading manufacturer of welding equipment and laser processing systems, announces it will showcase its latest welding, cutting and marking technologies at the Medical Design & Manufacturing (MD&M) West exposition and conference, to be held February 14-16, 2012 at the Anaheim Convention Center in California, booth #3051.
Miyachi Unitek will be displaying and demonstrating a variety of equipment ideal for the medical manufacturing market, including ultraviolet (UV) laser marker systems, laser and resistance micro welding systems, and a laser tube cutter. Also on display will be the Advanced Data Analysis Monitor (ADAM) weld monitor, and weld heads that offer stable, repeatable electrode force for a wide range of medical market resistance welding applications.
Miyachi Unitek's expert applications engineers will be conducting a program of daily in-booth demonstrations that will give attendees an opportunity to learn about Miyachi Unitek's newest cutting, welding, and marking capabilities and have their questions answered. Demonstrations will be held on Tuesday February 14th at 12.30 and 2.30p.m., February 15th at 10.30 a.m., 12.30 p.m., and 2.30 p.m., and February 16th at 10.30 a.m. and 12.30 p.m. Free light refreshments will be provided as part of the booth demonstration programs.
Miyachi Unitek will be demonstrating its UV (ultraviolet) Laser Marking System, which produces small characters on a wide array of materials and is ideal for marking plastics used in the medical and packaging industries. UV laser markers also offer extremely controlled metals marking, which results in the most reliable corrosion-resistant marking for medical materials.
"Miyachi Unitek's technology provides fast, reliable and corrosion resistant marking of medical devices," said Jack Lantz, president and CEO of Miyachi Unitek Corporation. "We have significant experience in the medical device industry and are eager to help manufacturers achieve UDI compliance."
Also on display is the Sigma Laser Tube Cutter gas assist fine laser cutting system, ideal for precision cutting of stainless steels, cobalt-chrome steel alloys, and Nitinol. The Sigma Laser Tube Cutter features high speed direct drive stages that maximize throughput. Multi axis options allow users to customize the tube cutter according to the cutting application for both on and off axis cut geometries. A user friendly interface with intuitive icons and customizable options provides easy navigation and programming for either program editing or execution.
Conference attendees looking for the best technology for small component welding can view a demonstration of Miyachi Unitek's LF Series Fiber Laser Micro Welding System, which offers extremely precise control and integration of the laser, tooling, and motion. The LF series can produce focused spot sizes down to 10 microns, while maintaining control of pulse width and peak power to enable fine micro welding.
For micro-miniature resistance welding, Miyachi Unitek's UB25 linear DC micro welder provides unsurpassed levels of control. The UB25 is ideal for smaller applications that require closed-loop feedback control and fast response times. Safety-critical applications such as those found in the medical markets will benefit from the UB25's precision low energy control. In addition, Miyachi Unitek will exhibit its 70 Series Servo-Motor Driven Weld Heads, which are designed for use in either automation or benchtop welding. These weld heads offer stable, repeatable electrode force for a wide range of medical market resistance welding applications.
Representing the very latest technology in resistance weld monitoring, Miyachi's Advanced Data Analysis Monitor (ADAM) will also be on display. ADAM not only monitors what happens during the weld, but also what happens before the weld is triggered, offering a 360-degree view of the process. Sophisticated SPC capabilities such as the integrated database and Minitab 15® statistical software enable customers to analyze and collect data. Other key features include current, voltage, power, resistance, force and cover gas flow monitoring; high resolution sensors; pre-and post-trigger viewing; envelope limits; and Ethernet communications capability. ADAM offers information to support ISO, GMP and TQM requirements.
For more information on Miyachi's technology for the medical device market, please visit booth #3051 at MD&M.
About Miyachi Unitek
Miyachi Unitek is a leading manufacturer of equipment and systems for resistance welding, laser welding, laser marking, laser cutting, and hot bar reflow soldering and bonding. The company provides products to a wide range of markets, including the medical device, battery, electric vehicle, and solar industries, as well as the global electronics, automotive, and general industrial markets. Miyachi Unitek is an ISO9001 certified company. Contact Miyachi Unitek at its company headquarters, located at 1820 S Myrtle Ave., Monrovia, CA 91016, by phone at (626) 303-5676, or by email at info@muc.miyachi.com. Find out more about the company's products and services at www.miyachiunitek.com.
Featured Product
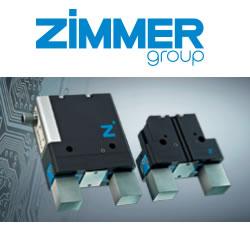
Zimmer Group - THE PREMIUM GRIPPER NOW WITH IO-LINK
IO-Link is the first standardized IO technology worldwide for communication from the control system to the lowest level of automation.