Secure hold using vacuum technology
With the PLANOS vacuum clamping system from SCHUNK, the competence leader for clamping technology and gripping systems, flat workpieces as well as those with a flat underside can be clamped on the machine table using vacuum simply, quickly and safely.
With the PLANOS vacuum clamping system from SCHUNK, the competence leader for clamping technology and gripping systems, flat workpieces as well as those with a flat underside can be clamped on the machine table using vacuum simply, quickly and safely. In order to further enhance the user flexibility, SCHUNK has recently introduced a standardized adapter plate by which the vacuum clamping system can also be used on MAGNOS magnetic chucks.
PLANOS consists of one or multiple combined matrix plates as well as a vacuum generator. During the clamping process, the workpiece is positioned and the vacuum is activated. In a matter of seconds the part is safely and precisely clamped in a level position with a height tolerance of +/- 0.02 mm. It can even secure thin plates precisely and deformation-free. Optional mechanical stops assist in the positioning and accommodate additional shear forces. The vacuum system has a modular design and can be expanded in a variety of ways. It can also be retrofit on existing systems. For this purpose, the matrix plate is secured to the machine table with a quick-change pallet system, clamping blocks, clamping claws or even using a magnetic chuck.
The standardized matrix plates with base bodies made of high-strength aluminum elements are available in the sizes 300 x 200, 300 x 400, and 400 x 600 mm and with grid sizes of 12.5, 25, and 30 mm. The suction surface and the required grid size can be determined depending on the workpiece geometry, the machining and the horizontal forces. The finer the grid, the stronger the holding force. In order to produce breakthroughs, a grid table suction device can be used for the 30 mm grid to elevate the workpiece in its position. On request, the SCHUNK matrix plates can also be equipped with friction pads which are automatically activated through the vacuum feed and permit higher shear forces. Compared with matrix plates without friction pads, the horizontal holding forces with friction pads are up to 30% higher. In the process, no additional force is exerted on the workpiece. The friction pads are resistant to oil and ozone and are individually replaceable if necessary.
To generate the vacuum, the innovative family-owned company offers special vacuum units to ensure maximum flexibility and process safety. They are equipped with an oil-lubricated vacuum pump and a liquid separator, which also serves as a vacuum accumulator. Various components for the system monitoring and interfaces for integration in the machine control ensure maximum safety. An emergency STOP function protects the vacuum pump against damage from suctioned liquids.
Featured Product
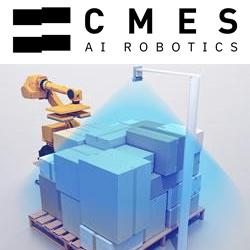