5-finger hand: Almost as talented as its human model
The 5-finger hand from SCHUNK enables service robots to carry out complex gripping operations and to communicate with gestures.
The ability expectations of Service Robots used in the domestic environment are high: They should intuitively adapt to the human, communicate in the usual human way and should even master complex gripping operations. With an Anthropomorphic Gripper Hand, SCHUNK the competence leader for clamping technology and gripping systems, is pushing hard to extend the development of humanoid service robots forward. The design study, which has been introduced at the International Expert Days on Service Robotics 2012, is available as a Right and Left "Hand" for the first time.
It is quite amazing how it resembles its human model, in size, shape, appearance and mobility. Nine drives enable the 5-finger hand to carry out various gripping operations. It has been found that many human gestures can be replicated, thus a visual communication between a human and service robot is simplified, therefore increasing the acceptance of using them in the domestic environment. By using tactile sensors in the fingers, the gripper hand has the necessary sensitivity and can therefore manage every gripping and manipulation task, even in unstructured and unforeseeable situations. Elastic gripping surfaces ensure a reliable hold of the gripped objects. The gripper hand can be connected with lightweight arms via defined interfaces, and SCHUNK has provided the LWA lightweight arm shown here. Christopher Parlitz, Manager for Service Robotics at SCHUNK has said," The 5-finger hand offers new approaches to the research in the field of service robotics in the immediate environment of humans. Studies on human-robot communication show that due to the gesticulating hand, new strategies can now be explored, since the hand allows a realistic form of nonverbal communication".
Featured Product
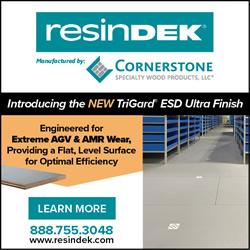