Schneider Electric introduces PacDrive 3 with Sercos III
Schneider Electric introduces PacDrive 3 with Sercos III, a fully integrated safety solution, and a new drive design. The engineering tools, which are now integrated into SoMachine Schneider Electric's software development environment, offers many new ways to reduce engineering time.
For years, PacDrive control technology has allowed users to have synchronized multiaxis motion, PLC functionality, and robotic control on a single hardware platform. This open technology utilizing international standards is aimed at reducing hardware and software complexity. Schneider Electric's consistent objective has been to hold the line against rising mechanical engineering costs in design, installation, and commissioning. PacDrive 3 opens up new possibilities for achieving this goal, while also introducing new technological approaches for long-term viability.
New communications concept
The PacDrive LMC 300 C, 400 C, and 600 C controllers offer scalable performance and can synchronize more than 100 servo axes. The LMC 101 C and 201 C controllers, compact new units for applications with eight and fewer synchronous axes, are also scheduled for release soon. The primary distinguishing feature of this generation is the changeover from the Sercos II motion bus to the fully integrated, Ethernet-based Sercos III bus:
Sercos III is the universal PacDrive 3 automation bus for servo drive and field communication as well as safe communication. Sercos III is a true standard, it does not rely upon a specific manufacturer, and it is one of the most powerful Ethernet-based communication solutions currently on the market.
In addition to the Sercos III interface, all controllers are equipped with an on-board CAN interface, standard Ethernet interface, and serial interface. The LMC x00C controllers have a Profibus and a Real-time interface (Profinet or Ethernet/IP) as well. Two free slots provide space for additional field bus and Realtime Ethernet interfaces. In addition to Sercos III and standard Ethernet, LMC x00C controllers can simultaneously operate up to four communication protocols (up to three Realtime Ethernet protocols plus one field bus protocol). When operating two field bus protocols simultaneously, at least one additional Realtime Ethernet protocol is possible.
Lexium LXM 62 is the completely new multi-axis servo drive design for PacDrive 3. The alternative multi-axis solution for PacDrive 3 consists of ILM servo modules, servo motors with integrated drives and shared power supply that are already familiar to users of the PacDrive M series. New stand-alone LXM 52 Series servo drives will also be added.
The Lexium LXM 62 servo drives consist of single drives (1 axis) and double drives (2 axes) connected to one or more shared power supplies, which can also power ILM servo modules. The double drives make compact, cost-effective servo drives possible. Pluggable interconnects and the replacement of backplane connections with quick-connect front-side slides also help to reduce installation costs.
As an alternative to the modular, multi-axis servo drive design of the Lexium LXM 62 Series, the soon-to-be-released Lexium LXM 52 stand-alone servo drives with integrated power supply offer cost-effective servo solutions for compact applications with fewer servo axes.
One engineering tool, one project
SoMachine Motion is the new software development environment for the entire PacDrive 3 engineering process. SoMachine Motion includes tools for motion system design, drive selection, program development, HMI applications, commissioning, diagnostics, and data handling in a single package. It also integrates a Safety Editor that meets IEC 61131-3 requirements for safety automation software development.
EPAS, SoMachine Motion's central software development tool, is already based upon CoDeSys V3, and offers the groundbreaking potential of object-oriented programming. Also now available is the EPAS plug-in EDESIGN. This tool, a first release of the planned centerpiece of a new method for graphically structuring machine functions, will further simplify software engineering.
SoMachine Motion can also be used for converting development projects that involve machines automated with PacDrive M. All of the previous work remains intact, and software that was developed for modular machine designs can be reused even when the system is changed to PacDrive 3.
The open safety concept of PacDrive 3 (safety pursuant to IEC 61508:1998, EN/ISO 13849:2006, and EN 62061:2005) meets the requirements of the new Machinery Directive 2006/42/EC, and takes a cutting-edge approach. Whether the need is for a fully integrated solution or a simple design with dedicated cabling, this concept offers a wide range of flexibility to meet individual requirements. In the integrated solution, a PacDrive safety PLC communicates with all relevant nodes at the drive and I/O levels via the Sercos III bus. Safety terminals are used to incorporate communication with sensors and actuators. With the integrated safety solution, users can implement safety functionalities up to SIL 3 in accordance with IEC 61508.
SoMachine Motion will offer a configuration and programming tool for creating the safety configuration and developing software for safety automation. This tool also includes comprehensive diagnosis and documentation functions. The PacDrive safety solution as a whole has been designed and built based upon the latest safety standards, and allows machine manufacturers to easily receive certification under the new European Machinery Directive in effect since December 2009.
Complete automation solutions
PacDrive 3 is part of the multicontroller platform of MachineStruxure, Schneider Electric's solution for machine builders. Thanks to interoperability between MachineStruxure and products from the comprehensive Schneider Electric portfolio, the company can offer complete solutions from a single source to meet the needs of the machine building and consumer goods sectors. As one of the world's largest manufacturers of equipment for electrical power distribution and industrial control and automation, Schneider Electric offers an extensive line of data acquisition systems and sensors, as well as standard and auxiliary electrical equipment for machine construction, production lines, and entire production facilities.
Schneider Electric Automation
Schneider Electric Automation GmbH, with headquarters in Marktheidenfeld and Seligenstadt, is part of the Schneider Electric Group. Within its Machine Solutions, Plant Solutions, and System Consistency divisions, the company specializes in the development and production of hardware and software products for automation solutions in machine building and plant engineering. From its location in Marktheidenfeld, the Machine Solutions division also controls its international activities within the corporate group.
Featured Product
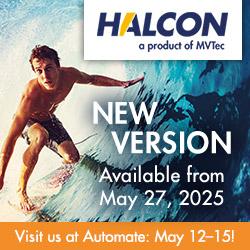