Opdi-Tex releases Stereo Camera with Sercos Interface
Complex machines and systems require numerous sensors to detect the orientation and position of system parts and/or products. Conventional image processing systems are often too slow and inflexible if adaptable arrangement of measuring points and easy system conversion are required.
Complex machines and systems require numerous sensors to detect the orientation and position of system parts and/or products. Conventional image processing systems are often too slow and inflexible if adaptable arrangement of measuring points and easy system conversion are required. Opdi-Tex\'s stereo camera offers numerous options for production and tool monitoring. It may be used as a stereo camera with pattern recognition or as a multiple photoelectric switch, replacing up to 30 photocells at once. Unlike common reflex switches, the camera is able to detect and track the distance to an object. The complete two-eye camera system contains integrated multi-color LED illumination with a special controller for a fully synchronized image acqusition from both cameras.
Without moving parts this camera is very suitable for use in industrial environments. Communication with machines and systems takes place via a Sercos interface with the stereo camera responding like a sensor.
About Sercos
Sercos is one of the world's leading digital interfaces for communication between controls, drives, and decentralized peripheral devices. Sercos has been used in machine engineering for more than 25 years and is implemented in over 500,000 applications with around 3 million real time nodes. The latest generation, Sercos III, can be used as a universal automation bus for machine production and system implementation.
Featured Product
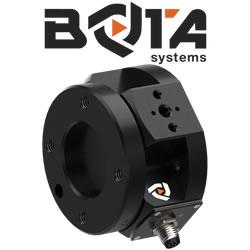