Rapid workpiece change on milling/turn centers
The VERO-S NSL turn clamping station from SCHUNK, the competence leader for clamping technology and gripping systems is a real productivity booster for milling/turning centers.
The VERO-S NSL turn clamping station from SCHUNK, the competence leader for clamping technology and gripping systems is a real productivity booster for milling/turning centers. It is based on the highly efficient VERO-S quick-change pallet system, and transfers the effect of the rapid workpiece change onto the lathe machining. By means of the patented double angled stroke, and the integrated turbo function, the NSL turn achieves pull-down forces of up to 125 kN, and holding forces of up to 375 kN. Therefore the clamping station from the innovative family-owned company ensures an extremely rigid and reliable clamping of devices and workpieces. A centering taper ensures a runout accuracy of less than 0.01 mm. Locking of the three or five integrated clamping modules is done via two clamping slides. It is self-locking and uses form-fit clamping. During machining the clamping station is unpressurized. Integrated springs provide for a permanent and secure clamping. For opening the locking, a pneumatic system pressure of 6 bar is sufficient.
Completely sealed
In order to increase the product life and process reliability, all functional parts such as base body, clamping pin, and clamping slide are made of hardened stainless steel. The maintenance-free modules are completely sealed and are reliably protected against chips, dust and coolant. A display shows the current clamping condition, and thus avoids errors before clamping. An intelligent plumbing of the module leaves enough space for bore holes on the base plate. Therefore the NSL clamping station can be used on all conventional machine types, and is suitable for speeds of up to 2.000 rpm. In size 450 three clamping modules are available for manual chucks of size 315. Size 570 offers more than five clamping modules for manual chucks up to size 630 mm.
Featured Product
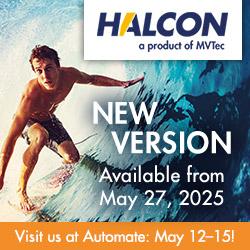