Wynright Introduces New Hybrid Light and Voice eFulfillment Materials Handling System
Innovative design improves productivity by allowing pickers to fill multiple discrete orders concurrently
ELK GROVE VILLAGE, Ill.--Wynright Corporation, a leading independent, U.S.-based provider of intelligent material handling systems, today announced the introduction of an innovative hybrid materials handling system for warehouse/distribution center eFulfillment that integrates pick to light and put to voice technologies into a single offering.
The hybrid system, for which Wynright has a patent pending, allows pickers to fill multiple orders at the same time rather than having to pick and put each order sequentially. Combining order fulfillment this way can help organizations realize up to a 25-percent increase in picking rates per hour - the equivalent of adding an extra person to an eight-hour shift.
"Pick to light and put to voice systems have been around for several years, and each type independently has its strengths and weaknesses," said Zane Daggett, General Manager, Selection Division at Wynright Corporation. "This is the first instance, however, where the two have been combined into an integrated system. While it seems simple, even obvious on the surface, it takes a lot of expertise in materials handling and these technologies specifically to make it work effectively."
In a standard warehouse or distribution center, pickers receive a single order, then pick the individual components from bins around the facility and put them in the tote for that order. For popular items, pickers may go to the same bin a dozen or more times each day. With Wynright's hybrid light/sound system, orders can easily be grouped together. The light system directs the picker to all the required bin locations and shows the aggregate quantity of items that should be picked for all the orders the picker is currently handling, and the voice system directs individual order quantities into which totes each product should be placed, saving time and increasing productivity. In addition, the hybrid light/sound system can be easily integrated into all standard warehouse management systems (WMS), further automating the process.
Wynright has designed the hybrid light/sound system to be very flexible to adjust to the capabilities of the workforce. For example, new employees may only be assigned two simultaneous orders, while experienced pickers may be responsible for a dozen or more orders on a single run. It can also be adjusted to accommodate faster picking in areas where lights are not available, such as end caps.
"This new system answers a growing need among large and mid-size enterprises (LMEs) that are being challenged to manage ever-higher volumes of smaller orders from online customers," Kevin Ambrose, CEO of Wynright Corporation said. "It's a great example of Wynright's solutions-based approach to materials handling."
About Wynright
Wynright Corporation is the nation's leading independent, U.S.-based provider of intelligent material handling systems. With more than 200 engineers in-house, the company designs, manufactures, integrates and installs the full spectrum of intralogistics solutions, offering both Wynright-branded and third-party equipment to meet customer needs. These include leading-edge conveyor and sortation systems, voice and light directed order fulfillment equipment, a suite of warehouse controls & execution software, robotics, mezzanines, and structures, all backed by critical round-the-clock service and support.
Since its founding in 1972, Wynright has been a trusted partner to some of the world's largest and fastest-growing companies, showing them how to use their space more efficiently to deliver improved productivity, today and tomorrow. For more information on our services, technology and product portfolio, please visit www.wynright.com.
Featured Product
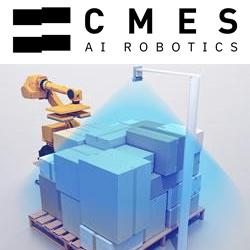
CMES - AI-Powered 3D Robot Vision
Powered by AI, CMES Robotics enables 3D vision for factory robots. CMES AI vision software enables robots to recognize unstructured, flexible, or deformed objects, pick them up, and loading and unloading. CMES Vision software has been deployed worldwide for random palletization and depalletization along with void filling applications. CMES Robotics automates your warehouse, logistics, and supply chain. For more information, please visit: cmesrobotics.com or email info@cmesrobotics.com.