RMT Robotics Announces Launch of New Layer Picking System
New tooling is capable of layer picking 95% of all consumer goods case configurations
(Grimsby, Ontario, Canada Sept. 17, 2012) - RMT Robotics® (www.rmtrobotics.com), a Cimcorp Oy company announces the development of its new layer picking system using its state-of-the-art, patent-pending robotic layer picking tool.
Using a combination of vacuum and clamping technology, the new tooling has the capability of picking 95 percent of consumer products on the market today including corrugate or boxboard cases, shrink wrap products, bottles, tubs and open trays. Patterns with voids and tier sheets are also handled with ease.
By incorporating the new tooling, RMT's layer picking system has the capability of picking multiple layers at once as well as picking and placing entire pallet loads, allowing for simple and secure inventory replenishment, especially with unstable loads.
"RMT takes great pride in our ability to engineer and design state-of-the-art robotic solutions to handle critical tasks in distribution centers where pick accuracy, reliability and cost effectiveness are paramount," said Derek Rickard, distribution systems manager, RMT Robotics. "The new layer pick tooling used in conjunction with RMT's high-speed gantry systems provides an ideal order picking solution for customers with a high-SKU inventory consisting of a wide variety of packaging types."
For more information, please contact Lori Vaughan, Marketing Coordinator, RMT Robotics, at lorivaughan@rmtrobotics.com.
For media information, please contact Kim Zdanowicz, Public Relations, Koroberi, Inc. (http://www.koroberi.com), by phone at +1 919-945-0548 or by email at kim@koroberi.com.
About RMT Robotics
RMT Robotics (www.rmtrobotics.com), a Cimcorp Oy Company, is a global company that manufactures and integrates turnkey robotic gantry-based order fulfillment and tire handling solutions designed to reduce operating costs and streamline operations.
Featured Product
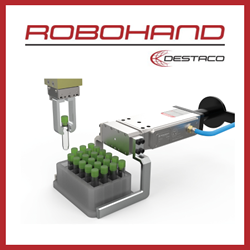
DESTACO - Revolutionizing Industrial Automation
Looking for a reliable solution to enhance your automation process? Look no further than the DESTACO Robohand Grippers. These grippers are designed for the modern world of robotics, offering unparalleled performance and precision. Whether you need to grip fragile items, irregularly shaped objects, or heavy-duty components, the DESTACO Robohand Grippers have got you covered. Their modular design allows for quick and easy customization, ensuring a perfect fit for your application.