Cyber Experts Engage on DARPA's Plan X
Proposers' Day dialogue cements program approach
When the team behind DARPA's Plan X mapped out where it wanted to go with research in the development of cyber capabilities and platforms, it knew the DARPA approach to problem solving included soliciting input from the leading experts in the field. On October 15 and 16, DARPA outlined its plans for Plan X to a packed house of potential developers and performers and solicited their feedback.
More than 350 software engineers, cyber researchers and human-machine interface experts attended the event. DARPA officials presented the goals of Plan X in preparation for release of the program's Broad Agency Announcement (BAA)-anticipated within the next month.
Plan X, announced in May 2012, is the first DARPA program of its kind. It will attempt to create revolutionary technologies for understanding, planning and managing DoD cyber missions in real-time, large-scale and dynamic network environments. Plan X will conduct novel research on the cyber domain. The Plan X program is explicitly not funding research and development efforts in vulnerability analysis or generation of cyberweapons.
"Insights obtained from discussions with government partners and potential performers during the Proposers' Day workshop will help us finalize our approach to the Plan X program," said Dan Roelker, DARPA program manager. "The program covers largely unchartered territory as we attempt to formalize cyber mission command and control for the DoD."
It is anticipated that the BAA for this effort will be posted to www.fbo.gov within the next month.
Featured Product
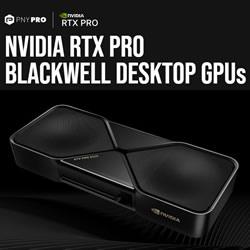
NVIDIA RTX PRO BLACKWELL DESKTOP GPUs
NVIDIA RTX PRO - Built for Professionals - NVIDIA RTX PRO™ Blackwell Desktop GPUs feature the latest breakthroughs in AI, ray tracing, and neural rendering technology to power the most innovative workflows in design, engineering, and beyond.