Northrop Grumman Maximizes Robotics and Automation to Reduce F-35 Center Fuselage Program Costs
Northrop Grumman's Palmdale site is a world-class facility that provides assembly, integration, testing and long-term maintenance capabilities for the F-35 and some of the world's other most advanced aircraft, including the B-2 Spirit and RQ-4 Global Hawk.
The Royal Australian Air Force's Chief of Air Force, Air Marshal Geoff Brown, met Northrop Grumman Corporation (NYSE: NOC) executives during a visit to the company's F-35 Lightning II production facility in Palmdale on Nov. 2. As part of his visit, Brown received an update on the F-35 program and observed the first F-35 center fuselage being manufactured at Palmdale for the Royal Australian Air Force as part of the low-rate initial production Lot 6.
The first inlet ducts were jig-loaded on Oct. 9. These will form the first of two Royal Australian Air Force F-35 center fuselages - denoted AU-1 and AU-2 - to be delivered in 2014 for pilot training.
Brown toured the Integrated Assembly Line (IAL) that produces the center fuselage. The IAL maximizes robotics and automation, providing additional capacity and assembly capability while meeting engineering tolerances not easily achieved manually. The IAL is one of the ways Northrop Grumman increases the program's affordability by reducing program costs and labor requirements.
"We were honored to host Air Marshal Brown here in Palmdale," said Michelle Scarpella, vice president of the F-35 program for Northrop Grumman. "He was able to see firsthand our advanced facility and manufacturing techniques that will help deliver the most advanced and most effective stealthy strike fighter to the Royal Australian Air Force."
In 2002, Australia joined the F-35 program. As one of eight international partners on the program, Australia has made significant contributions to the design and development phases of the program, and plans to purchase 100 F-35s.
As a principal member of the Lockheed Martin-led F-35 industry team, Northrop Grumman performs a significant share of the work required to develop and produce the aircraft. In addition to producing the F-35 center fuselage, Northrop Grumman also designed and produces the aircraft's radar and other key avionics including electro-optical and communications subsystems; develops mission systems and mission-planning software; leads the team's development of pilot and maintenance training system courseware; and manages the team's use, support and maintenance of low-observable technologies. In 2011, the company delivered 22 center fuselages and is on track to deliver 36 center fuselages this year. It will make its 100th delivery in early 2013.
Northrop Grumman's Palmdale site is a world-class facility that provides assembly, integration, testing and long-term maintenance capabilities for the F-35 and some of the world's other most advanced aircraft, including the B-2 Spirit and RQ-4 Global Hawk.
Featured Product
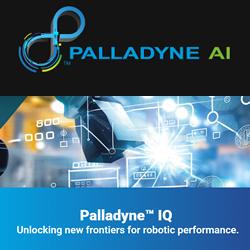