Electronics and High-Performance Computing Communities Sought for Microfluidic Cooling Demo
DARPA's ICECool seeks to demonstrate intrachip/interchip microfluidic cooling
The increased density of electronic components and subsystems in military electronic systems exacerbates the thermal management challenges facing engineers. The military platforms that host these systems often cannot physically accommodate the large cooling systems needed for thermal management, meaning that heat can be a limiting factor for performance of electronics and embedded computers.
DARPA introduced the Intrachip/Interchip Enhanced Cooling (ICECool) program in June 2012 to explore 'embedded' thermal management. The premise of ICECool is to bring microfluidic cooling inside the substrate, chip or package, including thermal management in the earliest stages of electronics design. One track of the program, ICECool Fundamentals, has already begun basic research into microfabrication and evaporative cooling techniques. Under the new ICECool Applications Track, DARPA now seeks performers from the electronics and high-performance computing (HPC) communities to demonstrate microfluidic cooling in monolithic microwave integrated circuits (MMICs) and embedded HPC modules.
"DARPA wants two things from this solicitation: ICECool concepts and techniques that can be readily integrated into the commercial off-the-shelf supply chain, and development and implementation of electrical-thermal-mechanical co-design techniques," said Avram Bar-Cohen, DARPA program manager. "To get there, we believe those already working with MMICs and HPC modules can add microfluidic cooling to established technologies. This is an open solicitation, and I encourage researchers within these communities and others to present their ideas."
The ICECool Applications broad agency announcement closes March 22, 2013. The solicitation may be found at: http://go.usa.gov/25qx.
DARPA chose MMIC chips and HPC modules as demonstrators because of their military relevance and previous Agency work with these devices. Microfluidic cooling for RF MMIC power amplifiers has the potential to dramatically reduce the size, weight and power (SWaP) requirements for a variety of RF systems like radar, communications and electronic warfare. DARPA has previously supported work with gallium nitride, a wide-bandgap material used for MMIC chips. Intrachip/interchip cooling methods may now improve the efficiency and output power of these devices.
Microfluidic cooling is also sought for HPC systems such as embedded computers that may be used for fire control and on-board data processing and fusing; such applications are performed by SWaP-sensitive systems. The Agency hopes that the demonstration of new cooling methods will complement the development of embedded, energy-efficient computing devices and architectures that is under DARPA's Power Efficiency Revolution for Embedded Computing Technologies (PERFECT) program.
Featured Product
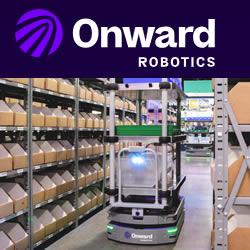
Onward Robotics - Meet Lumabot®
An interactive and powerful autonomous mobile robot for order fulfillment. Lumabot AMRs boost picking productivity and their human counterparts, intelligently moving material to the right person at the right time