SupplyChainBrain Interviews John Hayes of Seegrid Robotic Industrial Trucks
Robots create jobs and help move workers to better, higher paying, fulfilling, and safer jobs, according to John Hayes.
Pittsburgh, PA, April 4, 2013-John Hayes, National Account Manager for Seegrid, the robotic industrial truck leader was recently interviewed by Bob Bowman, Managing Editor of SupplyChainBrain. The video topic was Robots in the Warehouse: A Progress Report. Hayes explained how to eliminate risk by automating portions of a company's operation with simplistic automation.
Video Link: http://www.supplychainbrain.com/content/videos/2013-videos/promat-2013/robots-in-the-warehouse-a-progress-report/
Robots create jobs and help move workers to better, higher paying, fulfilling, and safer jobs, according to John Hayes. "Qualified workers are difficult to find. Automation doesn't take satisfaction away. Automation is empowering, by eliminating labor in some areas, taking some non-value-added activities out of the process,"
Hayes shared how companies, such as American Packaging Corp., based in Columbus, Wisconsin, implemented robotics with no reduction in labor, and increases in productivity, sales, job satisfaction (with an increased employee skill set), work environment safety, and wages. The company added 9% in manufacturing jobs as a result of its robotic investment.
Robots are motion-controlled automation. Automation and robots create jobs. When automation and robotics are discussed and applied without appropriate communications, they make some plant-floor workers worry about continued employment. Truth is (and this isn't necessarily intuitive when robots are first introduced to a site), automation saves manufacturing and other high-technology jobs. When automation is applied correctly, employees feel more valued and secure.
About Seegrid
Founded in 2003, based in Pittsburgh, Pennsylvania, Seegrid Corporation (http://seegrid.com) brings robotic vision-guided technology to the material handling industry. With more than thirty years of innovation and research by leading robotic scientists, engineers, programmers and logistics practitioners worldwide, Seegrid's exclusive Robotic Industrial Trucks are revolutionizing the movement of materials in manufacturing and distribution environments. Seegrid's technology transforms industrial vehicles into unmanned, automated pallet trucks and tow tractors that operate without the need for wire, tape, laser, magnet or other costly automated guided vehicle (AGV) guidance systems. Seegrid offers solutions that optimize workflow processes by increasing productivity and reducing costs, creating economic and operational advantages. Fast Company named Seegrid as one of the Top 50 World's Most Innovative Company in 2013 and among the Top 10 World's Most Innovative Robotics Company in 2013.Founded in 2003, based in Pittsburgh, Pennsylvania, Seegrid Corporation brings robotic vision-guided technology to the material handling industry. With more than 30 years of innovation and research by the leading robotic scientists, engineers, programmers and logistics practitioners worldwide, Seegrid's exclusive Robotic Industrial Trucks are revolutionizing the movement of materials in manufacturing and distribution environments. Seegrid's technology transforms industrial vehicles into un-manned, automated pallet trucks, tow tractors, and forklifts that operate without the need for wire, tape, laser or other costly automated guided vehicle (AGV) guidance systems. Seegrid offers solutions that optimize workflow processes by increasing productivity and reducing costs, creating economic and operational advantages.
Featured Product
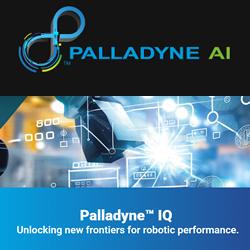
Palladyne™ IQ - Unlocking new frontiers for robotic performance.
Palladyne™ IQ is a closed-loop autonomy software that uses artificial intelligence (AI) and machine learning (ML) technologies to provide human-like reasoning capabilities for industrial robots and collaborative robots (cobots). By enabling robots to perceive variations or changes in the real-world environment and adapt to them dynamically, Palladyne IQ helps make robots smarter today and ready to handle jobs that have historically been too complex to automate.