BRM Announces NamPower Brush Tools for Fine Blanking; Industrial Brushes Help Manufacturers Automate Deburring and Surface Finishing
Brush Research Manufacturing (BRM), maker of the popular Flex-Hone® tool, announces NamPower™ abrasive disc brushes for fine blanking. NamPower™ industrial brushes remove metal burrs and impart an ideal surface finish at the same time, providing manufacturers with a cost-effective alternative to manual deburring and surface finishing.
Los Angeles, CA April 23, 2013
Brush Research Manufacturing (BRM), makers of flexible hones and industrial brushes, is announcing NamPower™ brush tools for fine blanking, a manufacturing method for making high-volume, high-precision parts. As manufacturers in a wide range of industries are learning, NamPower™ abrasive disc brushes provide maximum burr removal rates and superior surface finishing at the same time.
NamPower™ industrial brushes also offer a cost-effective alternative to manual deburring and surface finishing operations. These high-quality BRM brush tools integrate easily with plant machinery, CNC machining centers, robotic cells, and transfer lines. From metal finishing prior to plating to deburring after fine blanking, BRM's NamPower brushes provide a total finishing solution.
Fine Blanking for High-Volume, High-Quality Parts Production
Fine blanking uses a combination of metal stamping and cold extrusion technologies to manufacture high-volume, high-precision parts. By using specially designed tooling and a triple-action hydraulic press, manufacturers can make metal parts with fully-sheared, straight-cut edges. Fine blanking is also used to manufacture components with small holes, excellent flatness, and thin web sections.
Fine blanking is highly repeatable with little dimensional variation. Invented nearly 100 years ago, this highly-precise manufacturing process is now used to mass produce power tools, multi-tool components, and knife blades. Industrial applications for fine blanking tooling and fine blanking presses include the production of electronic components and auto parts.
Fine Blanking Dies and Quality Control
Fine blanking equipment produces parts with near-zero clearance and precise tolerances. Over time, however, the dies wear out and impart sharp edges to metal surfaces. These extruded edges often contain burrs, unwanted pieces of metal that can injure material handlers, damage seals, increase mechanical wear, interfere with lubrication, and lead to premature part failure. Metal burrs that break free from fine blanked parts can also damage machinery and equipment.
NamPower Abrasive Disc Brushes for Automated Deburring
For the high-volume production of fine blanked auto parts and electronic components, manufacturers need a cost-effective alternative to hand tools. That's why Brush Research Manufacturing (BRM) offers NamPower™ abrasive disc brushes, professional-grade deburring tools for automated machinery, CNC machining centers, transfer lines, and robotic cells.
Made with a molded, fiber-reinforced thermoplastic base, these high-quality industrial brushes are designed for use with a flow-through coolant holder. By allowing coolant to flow from the brush center instead of supplying lubricant only from the outside, NamPower™ arbors also provide improved cutting action and longer tool life.
Surface Finishing Solutions for Manufacturing
NamPower brush tools enable fine blankers to perform deburring and surface finishing operations at the same time. Parts manufacturers can also use NamPower abrasive disc brushes for edge radiusing, parts cleaning, and rust removal. From metal finishing prior to plating to deburring after fine blanking, BRM's NamPower brushes provide a total finishing solution.
About Brush Research Manufacturing
Brush Research Manufacturing (BRM), makers of the Flex-Hone® tool, is located in Los Angeles, California. Since 1958, BRM has been solving difficult finishing problems with brushing technology. BRM's Flex-Hone® tool is the standard against which all other surface finishing tools are compared.
Featured Product
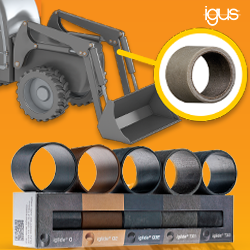
igus® - Free heavy-duty plastic bearings sample box
The iglide® heavy-duty sample box provides a selection of five unique iglide bearings, each suitable for use in heavy-duty equipment due to their self-lubricating, dirt-resistant properties. Each bearing material boasts unique benefits and is best suited for different application conditions, though each can withstand surface pressures of at least 11,603 psi at 68°F.