XYZ Robotic Arms for Assembly Automation from IntelLiDrives, Inc.
Multi-Axes Robotic System with Linear Servo Motors
Philadelphia, PA June 28, 2013
IntelLiDrives, Inc. newly released multi-axes robotic arms feature Linear ServoSlides - direct drive linear servo motor actuators - for exceptional repeatability and throughput.
Linear ServoSlide is a pre-engineered linear motor stage, designed to eliminate backlash, friction and wear problems associated with the mechanical transmissions, such as ball/lead screws, rack & pinion and gearboxes
Linear ServoSLide linear actuator features brush-less non-contact linear motor design with low cogging for fast and accurate positioning. Double rail bearing system is integrated into the slide to support moving carriage and to provide dynamic stiffness and precise straightness of travel.
Precision non-contact linear position feedback with selectable resolution from 0.1 to 10 microns is mounted in the carriage to minimize thermal drift. Limit Sensors are incorporated to establish end of travel and "home" positions.
Linear actuator components are mounted in the high strength extruded aluminum housing precisely machined to provide outstanding straightness and flatness for installation in horizontal or vertical orientations.
Linear ServoSLide incorporates connector panel to provide "plug-in" connectivity and quick disconnect for all signal and power requirements as well as cable transport module with high flex robotic cable installed and pre-wired to the connector panel.
Rotary table can be integrated with these XYZ robots to provide 4 degrees of freedom for the tool end effector.
IntelLiDrives, Inc. offers a wide range of servo amplifiers and advanced motion controllers to provide complete, integrated rotary system package.
Applications:
*semiconductor manufacturing
*electronic assembly
*medical manufacturing
*lab automation
*assemblyrobotics
About company:
IntelLiDrives, Inc. manufactures comprehensive line of direct drive linear and rotary actuators used in electronic assembly, semiconductor manufacturing, life sciences and general motion automation applications.
Featured Product
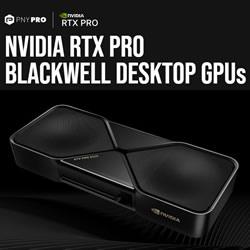
NVIDIA RTX PRO™ BLACKWELL DESKTOP GPUs
NVIDIA RTX PRO™ - Built for Professionals - NVIDIA RTX PRO Blackwell Desktop GPUs feature the latest breakthroughs in AI, ray tracing, and neural rendering technology to power the most innovative workflows in design, engineering, and beyond.