Universal Robotics Introduces Breakthrough Neocortex Technology for Logistics Industry; Unlimited Depalletization Accelerates Unloading and Improves Safety
Universal Robotics Inc., a leader in 3D flexible automation, introduces Neocortex, next generation artificial intelligence software, for unlimited box handling and depalletizing in logistics operations. It automates on-the-fly handling of all cartons of any size and shape without advance analysis with less than a 24-month payback.
Nashville, TN July 24, 2013
Universal Robotics Inc.®, a leader in 3D flexible automation, introduces the first flexible intelligence software for unrestricted box handling in logistics operations. The Unlimited Depalletization Application automates on-the-fly handling of all cartons of any size and shape without advance analysis. Benefits include faster unloading, increased safety and less than 24-month payback.
Ground-Breaking Logistics Results
This breakthrough application focuses on box handling areas in the supply chain long considered too chaotic for robotics. It offers significant potential for improving worker safety and operations quality.
"Today's manual unloading processes can lead to injured workers, inconsistent unload rates and product damage. Our new unlimited depalletization software changes that," said David Peters, CEO, Universal Robotics. "Companies will increase both safety and efficiency through technology which handles every carton, sight unseen. Truly unlimited depalletization is now a reality."
Built on Universal's Neocortex Platform, Originally Developed with NASA
The application leverages the machine learning, big data software platform called Neocortex® that Universal Robotics has been commercializing for three years. Neocortex intelligence software, based on technology originally co-developed between NASA and Vanderbilt University, was created to handle random situations. When applied to the unloading process, it enables fast and flexible identification of any box, independent of size or condition, weight, orientation within the work cell, label quantity/type or box graphics or color.
Key features include:
*Fast-up to 1,400 cases per hour
*No boundaries-unlimited cartons never seen before
*Adaptable-moves cases in any position or orientation or even damaged
*Versatile-any color of boxes with any combination of labels
The newly released Neocortex works seamlessly with Universal's Spatial Vision® Robotics 3.2, which provides scalable real-time 3D vision guidance for any robot using off-the-shelf cameras, sensors and lasers.
Tested with Popular Robot at Fortune 200 Distribution Center
Neocortex software can be integrated with any hardware. For instance, to create a highly flexible solution, Universal Robotics worked closely with the Motoman Robotics Division of industry leader Yaskawa America Inc. over the past three years. The company provided technical expertise and several dual arm and single arm robots for testing, including contributing the Motoman MPL80 palletizing robot for the final testing at a Fortune 200 logistics center.
"Spatial Vision Robotics 3.2 with its underlying Neocortex artificial intelligence represents a significant breakthrough in perception technology which was needed for robotics to be utilized in warehouses and fulfillment centers," said Roger Christian, Vice President, Yaskawa America, Inc. "Being able to recognize and locate random products in real-time enables our robots to become a useful tool to lower labor costs in the logistics market."
For more information, contact Universal Robotics at (615) 366-7281 or review these links: Unlimited Depalletization Application and Neocortex 3.2.
Featured Product
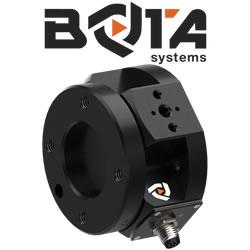
Bota Systems - The SensONE 6-axis force torque sensor for robots
Our Bota Systems force torque sensors, like the SensONE, are designed for collaborative and industrial robots. It enables human machine interaction, provides force, vision and inertia data and offers "plug and work" foll all platforms. The compact design is dustproof and water-resistant. The ISO 9409-1-50-4-M6 mounting flange makes integrating the SensONE sensor with robots extremely easy.
No adapter is needed, only fasteners! The SensONE sensor is a one of its kind product and the best solution for force feedback applications and collaborative robots at its price. The SensONE is available in two communication options and includes software integration with TwinCAT, ROS, LabVIEW and MATLAB®.