ABB Robotics Pack Expo 2013 exhibit highlights new 8 kg IRB 360 FlexPicker and comprehensive Palletizing portfolio
New FlexPicker model expands high speed picking and packing of industry leading Delta robot to heavier items and larger product groupings
AUBURN HILLS, Mich. - ABB Robotics, a leading supplier of industrial robots, is exhibiting two fully operational, multi-robot demonstration cells at Pack Expo 2013, September 23-25 at the Las Vegas Convention Center (Booth # C-4113).
The two cells accentuate ABB's complete line of packaging robots, highlighted by a high speed robotic picking demonstration featuring the new 8 kg IRB 360 FlexPicker model, which expands the high speed picking and packing performance of the most widely used Delta robot in the industry to heavier items. Also featured is a cell displaying the performance and versatility of ABB's comprehensive palletizing portfolio, and robotic software that reduces programming complexity and creates an intuitive human machine interface for production operation.
The ABB exhibit also includes a robotic cell displaying a wide array of machine safety equipment from ABB JOKAB SAFETY, part of the ABB Low Voltage Products division; and automated machine and motion control products from ABB's Discrete Automation and Motion division.
Further detail on the ABB Pack Expo 2013 booth displays:
High Speed Picking Demo
The centerpiece of the high speed picking demo is the new 8 kg IRB 360 FlexPicker with a Schmalz vacuum gripper, simulating a carton loading application by picking five liquid filled plastic bottles in a single cycle, and placing them on a conveyor. A 1 kg FlexPicker model uses vision guidance and conveyor tracking to individually pick the randomly positioned bottles off the conveyor, and place them in uniform groups back on the initial conveyor to continue the loop. Both FlexPicker models utilize ABB's PickMaster 3 software, which integrates conveyor tracking, advanced vision guidance and vision inspection capabilities in an easy-to-use programming platform.
The 8 kg (1130mm work range) FlexPicker provides a robust solution for handling both heavier individual products and larger product groupings in multi-pick applications, with the ability to handle up to 500 products per minute. The 8 kg model is available with the FlexPicker's sanitary options, including a hygienic design for wash down applications, and an IP69K rated stainless model. Along with the existing 1 kg (1130mm and 1600mm work range) and 3 kg (1130mm) variations, and the soon to be introduced 6 kg model in the 1600mm work range, the expanded FlexPicker portfolio provides end users the broadest portfolio of high speed picking robots available in the industry.
Palletizing Demo
The robotic palletizing loop demonstrates the palletizing and depalletizing of varying formats of corrugated cases utilizing two of ABB's dedicated palletizing robots. The demo begins with the IRB 760 robot picking rows of corrugated boxes off an infeed conveyor, and, once it has secured a full three-row box layer, it places the layer on a pallet. A high speed, compact IRB 460 robot depalletizes the pallet a row at a time, placing the boxes back on the infeed conveyor to keep the whole sequence in constant motion.
The IRB 760, designed for high-throughput, full-layer palletizing and depalletizing, is equipped with a Schmalz vacuum layer gripper. With a payload capacity of 450 kilograms and a reach of 3.2 meters, it features a high inertia wrist - double that of competitors - that enables it to handle heavier and larger product and tooling payloads faster than any other robot in this class. The IRB 760 robot is programmed using Robot Studio Palletizing PowerPac software, which combines two prominent ABB software technologies - RobotStudio and the Palletizing Power Pac - into a single bundle.
The IRB 460 (4-axis, 110 kg payload, 2.4m reach) robot is specifically designed to meet the high throughput requirements of end-of-line and bag palletizing applications. The IRB 460 in the demo utilizes a 10-zone ABB Vacuum FlexGripper, capable of securing and moving multiple boxes in one cycle. The accompanying PalletPack 460 PalletWare software package configures a complete palletizing system via the configuration wizard on the robot's FlexPendant, eliminating the need for traditional robot programming. PalletWare also provides a complete FlexPendant HMI for cell operation, and an integral ABB PLC controls the flow of product on the infeed conveyors, pallet conveyors and gripper operation.
Robot Controllers
Two ABB IRC5 controller variations are featured between the two robotic demo cells:
*The desktop sized IRC 5 Compact, controlling the two IRB 360 FlexPickers, provides the same industry leading functionality as the standard model in a portable unit, including superior motion control and user friendly FlexPendant programming.
*The standard IRC 5, ABB's fifth generation robot controller, is controlling the two Palletizing robots. It is available with ABB's MultiMove software which allows one controller to move up to 36 robot axes in fully coordinated motion to work collaboratively or independently on the same manufacturing system or packaging line.
ABB JOKAB SAFETY
The ABB JOKAB SAFETY cell, integrated with an IRB 1600 robot and IRC5 Controller, is equipped with a full array of safety features including a Pluto Safety PLC, Quick-Guard® Safety Fencing, Smile Tina E-stops, Safety Mats, Eden Safety Sensors, Safeball ™ Stations and Focus II Light Curtains.
Discrete Automation and Motion (DM)
Additional automated machine and motion control products from ABB's Discrete Automation and Motion (DM) division are on display, highlighted by the newly released Automation Builder software suite. Automation Builder is used to program the eCo micro PLC, the higher end extreme condition capable AC500 PLC with integrated machine safety and motion control capability using the PLCOpen motion control standard, human-machine interfaces, and robotics integration all in one integrated software suite. This allows ABB to provide a complete machine architecture including safety products, motors, VFD's, motion control, PLC's, HMI's, and robotics.
About ABB
ABB is a leader in power and automation technologies that enable utility and industry customers to improve their performance while lowering environmental impact. The ABB Group of companies operates in around 100 countries and employs about 130,000 people.
About ABB Robotics
ABB Robotics is a leading supplier of industrial robots - also providing robot software, peripheral equipment, modular manufacturing cells and service for tasks such as welding, handling, assembly, painting and finishing, picking, packing, palletizing and machine tending. Key markets include automotive, plastics, metal fabrication, foundry, electronics, machine tools, pharmaceutical and food and beverage industries. A strong solutions focus helps manufacturers improve productivity, product quality and worker safety. ABB has installed more than 200,000 robots worldwide.
Featured Product
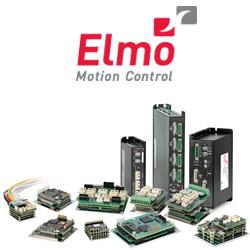
Elmo Motion Control - The Platinum Line, a new era in servo control
Significantly enhanced servo performance, higher EtherCAT networking precision, richer servo operation capabilities, more feedback options, and certified smart Functional Safety. Elmo's industry-leading Platinum line of servo drives provides faster and more enhanced servo performance with wider bandwidth, higher resolutions, and advanced control for better results. Platinum drives offer precise EtherCAT networking, faster cycling, high synchronization, negligible jitters, and near-zero latency. They are fully synchronized to the servo loops and feature-rich feedback support, up to three feedbacks simultaneously (with two absolute encoders working simultaneously). The Platinum Line includes one of the world's smallest Functional Safety, and FSoE-certified servo drives with unique SIL capabilities.