Rockwell Automation Launches New Power Monitoring Solutions
Irregularities in incoming power can negatively impact discrete and process applications' electronic components and the bottom line. Rockwell Automation has expanded its Allen Bradley power-quality portfolio to now include the i-Sense monitoring solution, i-Grid service and DySC dynamic sag corrector. These scalable solutions help OEMs and end users identify and mitigate power issues to improve uptime and productivity.
"Power-quality issues are responsible for a significant amount of unplanned downtime, yet power quality is often overlooked as a key productivity variable," said Scott Harlan, product manager for power-quality portfolio, Rockwell Automation. "Our new monitoring and mitigation solutions help identify where and when voltage sags and outages occur, and offer corrective actions to improve performance."
Improved monitoring - The first step toward improved performance is identifying any power-quality issues affecting electronic equipment. The i-Sense voltage monitors read incoming power for the entire facility. The cost-effective, maintenance-free i-Sense technology provides vital data that pinpoints voltage-based power events, reveals any consequent relationship between voltage sags and downtime situations, and helps users get operations running with minimal mean time to repair (MTTR).
Real-time analyzing - The subscription-based i-Grid service logs, analyzes and corroborates i‑Sense data via an Ethernet or modem connection from in and around facilities to confirm if power-quality issues were the result of a grid event. Service options include detailed technical analysis and executive summaries. The i-Grid service also can send instant notifications to facility managers that a power event has occurred, enabling them to more quickly diagnose downtime and resume operations.
Proactive protection - Data collected from the Rockwell Automation installed base of several thousand i-Sense units suggests that most downtime events are the result of short-duration voltage sags, commonly lasting less than 0.1 seconds. While barely perceptible, these sags can impact the performance of electrical equipment and the facility as a whole. The DySC dynamic sag corrector uses patented, double-conversion inverter technology to protect against brief voltage sags and momentary outages. Customers can scale the DySC corrector from 0.25 kVA to 2000 kVA, offering machine- to facility-wide protection. The corrector provides 100 percent sag protection in a relatively compact size and without batteries, compressors, pumps or flywheel bearings. Optimized for fast response at voltage peaks, the DySC corrector has a typical peak voltage detect time (pVdT) of one millisecond and can provide a facility continuous, uninterrupted power for up to five seconds.
The Allen-Bradley power-quality portfolio reaches beyond the new solutions to meet the needs of customers at every level and stage. The Allen-Bradley PowerMonitor 5000 monitor provides current, power factor flicker, waveform capture, harmonic analysis and sub-cycle transient detection. The Allen‑Bradley PowerPad Portable PowerMonitor unit offers a portable, self-contained solution, enabling monitoring anywhere in the facility. Allen-Bradley surge and filter products mitigate transient and noise problems at a machine level and uninterruptable power supplies (UPS) provide backup power to keep critical control and network circuits operating through a power interruption.
About Rockwell Automation
Rockwell Automation Inc. (NYSE: ROK), the world's largest company dedicated to industrial automation and information, makes its customers more productive and the world more sustainable. Headquartered in Milwaukee, Wis., Rockwell Automation employs over 22,000 people serving customers in more than 80 countries.
Source: https://www.rockwellautomation.com/
Featured Product
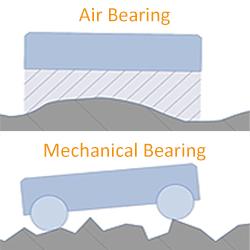