Navy 'Mine-Hunter' AUV Sets Mission Endurance Record
The fully autonomous endurance mission was designed to push the boundaries of traditional AUVs with the objective to uncover the challenges and requirements for significantly extending AUV endurance for new applications.
WASHINGTON--The U.S. Naval Research Laboratory's (NRL) Acoustics Division, with Bluefin Robotics, executed a record setting 507 kilometer (315 mile), long-endurance autonomy research mission using its heavyweight-class mine countermeasures autonomous underwater vehicle (AUV), Reliant.
NRL's Reliant AUV, when equipped with a low frequency broadband (LFBB) sonar system, is perhaps best known as the prototype for the new U.S. Navy Knifefish mine-hunter.
Navigating from the waters of Boston Harbor, the 20 foot long, 1,350 pound, 'heavyweight' AUV traveled south past Cape Cod, headed west through Nantucket Sound between Martha's Vineyard and the mainland, and then continued south of Long Island to the approaches to New York City. The fully autonomous endurance mission was designed to push the boundaries of traditional AUVs with the objective to uncover the challenges and requirements for significantly extending AUV endurance for new applications.
To optimize for endurance and range, the vehicle traveled at a depth of 10 meters and an average speed of 2.5 knots through busy waterways and strong currents. The vehicle surfaced at 20-kilometer intervals to report position via Iridium satellite and made Upper New York Bay with a 10 percent energy reserve crediting a new high capacity energy section.
"This record multi-day research mission demonstrates the state-of-the-art autonomy methods and capabilities of the Reliant AUV," said Dr. Brian Houston, head, NRL Physical Acoustics Branch. "It is our first step in developing a robust autonomy paradigm for AUVs in long endurance scenarios."
Reliant uses a modular vehicle design that was recently configured with a 40 kilowatt-hour (kWh) energy section that enabled the 109-hour journey. The AUV is navigated using a fiber-optic gyro based inertial navigation system (INS) integrated with GPS, and a Doppler velocity log (DVL) providing precise underwater navigation for long endurance missions.
This exercise is the first of several planned missions that will incrementally increase autonomy complexity and endurance over the life of NRL's research program and in overall AUV-based technology for the Navy.
Houston and his team are developing AUV based technologies that include extension of the Knifefish technology (as part of the Office of Naval Research Future Naval Capabilities program), increasing ranges for mine countermeasure (MCM) operations, and advancing autonomy for AUVs. Houston's team is also applying this new technology to shallow water Anti-Submarine Warfare (ASW). This more recent development provides the Navy with the technical foundation for high performance detection and classification of difficult ASW targets using active sonar on AUVs in challenging environments.
The purpose of the system is to address the Navy's need to reliably detect and identify undersea volume and bottom mines in high-clutter environments with low false alarm rates. The Knifefish system is a part of the Littoral Combat Ship (LCS) mine countermeasure (MCM) mission package targeted to reduce risks to personnel by operating in potential minefield regions as an off-board sensor, allowing host ships to remain at safe distances outside minefield boundaries.
The Naval Research Laboratory is the Navy's full-spectrum corporate laboratory, conducting a broadly based multidisciplinary program of scientific research and advanced technological development. The Laboratory, with a total complement of nearly 2,500 personnel, is located in southwest Washington, D.C., with other major sites at the Stennis Space Center, Miss., and Monterey, Calif. NRL has served the Navy and the nation for 90 years and continues to meet the complex technological challenges of today's world. For more information, visit the NRL homepage or join the conversation on Twitter, Facebook, and YouTube.
Featured Product
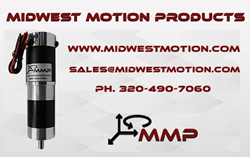
Midwest Motion Products is a leading provider of robust and reliable Motion Control Products.
MMP specializes in supplying high-quality Brushed & Brushless DC Motors & Gearmotors for Robotics and Automation Equipment with a wide range of motor windings and gear ratios. With an impressive track record of more than 8,000 released DC Gearmotors designs and over 2,000,000 individual part numbers, we are renowned for our ability to handle large-scale orders. Due to our huge on-hand inventory, we are also well known for lightning-fast delivery of our standard products. We take pride in our dedicated customer service and our team of knowledgeable sales and engineering experts who are ready to assist you with custom design solutions tailored to your specific application. Additionally, we also offer a wide range of complimentary products, such as DC Motor Controls, DC Linear Actuators, AC-DC power Supplies, and DC Servo Amplifiers and others.