Velodyne LiDAR Technology Wins Big in China 'Future Challenge'
Top eight finishers in 23km road test rely on company's 3D LiDAR sensors to guide their intelligent vehicles.
Morgan Hill, CA November 25, 2013
When the dust settled on China's fifth annual Future Challenge earlier this month - pitting intelligent vehicles against each other on a course designed to test their capabilities -- Velodyne's 3D LiDAR technology (http://www.velodynelidar.com) was on board all of the top eight finishers.
In all, eleven unmanned vehicles designed primarily by Chinese universities - and one South Korean institution -- competed in the challenge, in Changshu, Jiangsu Province. The race was organized by the National Natural Science Foundation of China (NSFC), as part of its Cognitive Computing of Visual and Auditory Information initiative.
Velodyne's proprietary 3D LiDAR vision technology provides active sensing for crash avoidance, driving automation and mobile road survey and mapping. Velodyne HDL-64E and HDL-32E sensors deliver 360-degree views of the car's environment, with real-time updates 20 times per second.
Vehicles were put through both suburban and urban road tests, over a 23-kilometer course. Cars on the course needed to demonstrate the ability to recognize light, eliminate human and vehicle interference, successfully detour around construction zones, turn around and come to a stop. All were also required to establish the ability to make a U-turn, accelerate and decelerate. Performance was graded on a "4s" scale: safety, smartness, smoothness and speed.
"This is simply a remarkable accomplishment," said Wolfgang Juchmann, PhD, Velodyne LiDAR Director of Sales and Marketing. "The Future Challenge course was nothing less than demanding throughout, with terrain and tests that demonstrated LiDAR's versatility and reliability in real time. And the fact that eight of eleven vehicles were so equipped stands as a huge vote of confidence in our technology."
A team from the Beijing Institute of Technology placed first, with a Military Transportation University team placing second and a Hefei Institutes of Physical Science, Chinese Academy of Sciences team placing third. Other competitors using LiDAR included Xi'an Jiaotong Universtiy, Tongji University, Tsinghua University, Nanjing University of Science and Technology and Wuhan University.
About Velodyne LiDAR
Founded in 1983 and based in California's Silicon Valley, Velodyne, Inc. is a diversified technology company known worldwide for its high-performance audio equipment and high-definition LiDAR sensors for autonomous vehicle applications. The company's LiDAR division evolved after founder and inventor David Hall competed in the 2004-05 DARPA Grand Challenge using stereovision technology. Based on his experience during this challenge, Hall recognized the limitations of stereovision and developed the HDL64 high-resolution LiDAR sensor. More recently, Velodyne has released its smaller, lightweight HDL 32E sensor, available for many applications including UAV's. Since 2007, Velodyne's LiDAR division has emerged as a leading developer, manufacturer and supplier of high-definition LiDAR sensor technology used in a variety of commercial autonomous vehicle applications, including 3D mapping and surveying. For more information, visit http://www.velodynelidar.com.
Featured Product
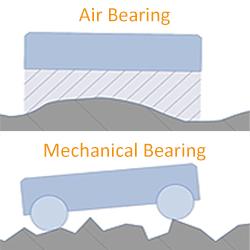
PI USA - Hexapods for 6-Axis Precision Automation
PI Hexapods simplify multi-axis alignment / positioning with a programmable pivot point, tool/work coordinate systems, virtual programming software.