Sandia to Exhibit Real-World Robotics Successes at DARPA Challenge
The challenge is focused on human-scaled robots that assist in humanitarian aid and disaster response.
Engineers from Sandia National Laboratories will demonstrate real-world robotics successes at the DARPA Robotics Challenge Trials 2013 Expo this week in Florida. The challenge is focused on human-scaled robots that assist in humanitarian aid and disaster response. Both the Robotics Challenge Trials and the Expo are open to the public, especially students, to encourage interest in science, technology, engineering and math.
Sandia National Laboratories' Gemini-Scout Mine Rescue Robot is equipped to handle any number of obstacles, including rubble piles and flooded rooms, and to help rescuers reach trapped miners safely and efficiently. (Photo by Randy Montoya)
Sandia's robotics program has been working closely with the Defense Advanced Research Projects Agency (DARPA) over the years to develop and deliver robots with the potential to save lives. Such technology keeps humans away from jobs that are dangerous, dirty and dull.
"We are pleased to be a part of DARPA's exposition," said Steve Buerger, Sandia robotics engineer. "Sandia specializes in working on major problems of national importance. We have produced robots that are out in the real world, being used for real applications. Sandia is in a position to develop life-saving solutions for applications that may be too low-volume or require technology that is too immature for industry to invest in."
Sandia engineers will demonstrate the Gemini Scout Mine Rescue Robot, which was designed to overcome dangers lurking in a mining accident: poisonous gases, flooded tunnels, explosive vapors and unstable walls and roofs. Such potentially deadly conditions and unknown obstacles can slow rescue efforts to a frustrating pace. The Gemini Scout system eliminates some of the unknowns and arms first responders with critical information. Less than 4 feet long and 2 feet tall, Gemini-Scout is nimble enough to navigate around tight corners and through 18 inches of water, crawl over boulders and rubble piles and move in ahead of rescuers to evaluate hazardous environments and help plan operations. In addition to giving rescuers an idea of where they're headed, the robotic scout can haul food, air packs and medicine to those trapped underground. It is equipped with two-way radios and can even be configured to drag survivors to safety.
The lifelike, cost-effective, robotic Sandia Hand, developed in 2012 to disable improvised explosive devices, will also be on display. The Sandia Hand addresses cost, durability, dexterity and modularity issues, all of which have prevented widespread adoption of other robotic hands. Earlier robotic hands cost more than $250,000, which was too expensive for wide distribution to troops, but Sandia's version costs $10,000 in low-volume production. The 95 percent cost reduction is an important breakthrough, but the Sandia hand is remarkable in many ways.
It is modular, so different types of fingers, such as flashlights, screwdrivers or cameras can quickly and easily be attached with magnets and quickly plugged into the hand frame. Modularity also provides durability; if the operator accidentally runs the hand into a wall or another object, the fingers are designed to fall off, rather than break, allowing rapid recovery.
Sandia's Urban Hopper robot also will be on display during the event. The first Hopper made history when it debuted in 1999 for its unique ability to hop 20 feet in the air over walls and other obstacles. With applications for planetary exploration, gathering intelligence in war and assisting police during standoffs or surveillance operations, the Hopper was the first robot powered by a combustion cylinder and a piston foot, and the wheeled Urban Hopper was the first hybrid hopping/wheeled mobility system.
http://www.sandia.gov
Featured Product
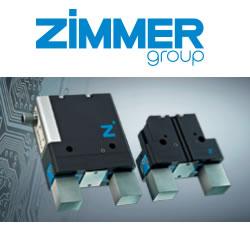
Zimmer Group - THE PREMIUM GRIPPER NOW WITH IO-LINK
IO-Link is the first standardized IO technology worldwide for communication from the control system to the lowest level of automation.