Festo Introduces the New CPX-FB36 Node for EtherNet/IP Communications
The CPX-FB36, which is the next generation replacement for the Festo CPX-FB32 communication node, is ideal for production and process automation environments requiring diagnostics from the operational and master controller level on down to the field level.
The CPX-FB36 brings new options and high performance to EtherNet/IP applications. New features include an integrated Ethernet switch that eliminates and/or reduces the need for external switches and thereby lowers cost. The new node supports line, tree, or ring topology for greater flexibility. It also supports device level ring functionality for robust, redundant network connections. It facilitates quick connect functionality for end-of-arm tooling and other quick change applications. For fast response times, Festo adopted a new processor design. Requested Packet Interval (RPI) settings now go as low as 1ms.
In addition to these new features, the CPX-FB36 offers industry leading diagnostic and function integration capabilities. For example, multiple pressure zones and power distribution zones allow the machine designer to use one manifold where multiple manifolds would otherwise be required. Galvanic-isolated power for electronics/outputs/valves allows connection to safety relays and systems. There is an integrated web server for diagnostic and parameter monitoring.
Advanced diagnostic capabilities for connected modules include:
•Short circuit protection and detection for individual
input and output channels, including solenoids
•Wire fracture monitoring for solenoids and connected
I/O
•Configurable de-bounce filtering to support a wide
variety of connected sensors
•Configurable signal extension for digital inputs
•Analog input and output modules with configurable
signal smoothing and limit monitoring
Functional integration, including integrated pressure sensors and proportional pressure regulators, communicate data in real world units (PSI, Bar, Kpa) for simplified HMI interactions.
Featured Product
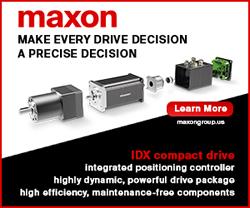