Manufacturers and Suppliers Turn to Coherix for Technology to Eliminate Flatness Quality Issues
While manufacturers and suppliers are facing a continued increase in production demands from 2013, they are also battling flatness quality issues. Companies are turning to Coherix ShaPix products to obtain a deeper understanding of their machined surfaces to mitigate problems.
Ann Arbor, MI January 15, 2014
A strong increase in sales at Coherix at the end of 2013 is continuing in 2014 due to production demands their customers are experiencing in the manufacturing of machined parts. The manufacturers and suppliers are turning to Coherix for technology to eliminate flatness quality issues. Manufacturers and suppliers have determined that a deeper understanding of their machined surfaces is needed to mitigate problems before they become compounded.
When asked about the company's take on flatness, Brad Pines, Coherix General Manager, states, "In 2013, we had an increase of industrial manufacturing customers come to us with the desire to simply understand their surfaces better. They wanted to improve their processes, gain more information about their parts and uncover the areas that needed attention. Flatness is an important specification - our goal is to improve and streamline the process of obtaining the complete surface information and empower our customers to make strategic improvements in their processes to ensure function."
These customers are using Coherix's ShaPix high-definition, high-speed 3D metrology systems, which capture and measure 4 million points of data on a planar surface in less than a minute. An easy to understand report and surface visualization are then generated which provide the manufacturer with an easy way to pinpoint problem areas. The manufacturer's goal is to eliminate the expensive consequences and production delays that can occur when the full surface measurement is not captured.
Manufacturers and suppliers have come to Coherix as a result of inconsistent functional parts, a lack of intuitive data and confusion when mitigating surface problems occurring in their processes. In an effort to solve these problems, ShaPix diverges from traditional metrology and uses multiwavelength interferometry to reconstruct the entire planar surface with 3D color height map visualizations. With fields of view ranging from 150mm x 150mm to 300mm x 300mm (and larger with full stitching capabilities) the ShaPix products are able to capture and process the data faster, easier and for a lower cost than traditional methods.
As a means of controlling surface shape to ensure functionality, a designer may call out a zone flatness specification. Zone flatness breaks the planar surfaces into smaller zones typically with tighter tolerances than the overall surface. These smaller zone areas having tighter tolerances enables designers to more closely describe the functional surface shape. By measuring the full surface of a part, ShaPix is able to evaluate the entire surface as well as any number of smaller zones on the surface without making assumptions.
For additional information on the flatness capabilities of ShaPix, please read the attached Engineering & Manufacturing Pain Relief document.
Coherix is a privately held, global supplier of high-speed, high-definition 3D visualization and inspection solutions designed to improve the management of manufacturing processes. Headquartered in Ann Arbor, the company has technical centers in Europe and the Asia Pacific region. Coherix products are being utilized around the world at companies such as Intel, Amkor, BorgWarner, Ford, Honda, Allison Transmission, Chrysler, General Motors, Micron, Infineon, John Deere, Volvo Technology Transfer and Aisin among others.
Featured Product
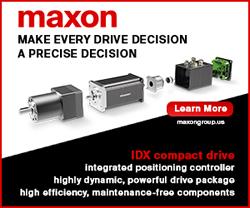
The maxon IDX Compact Drive with Integrated Positioning Controller
The compact brushless EC-i motor combined with an EPOS4 positioning controller delivers a highly dynamic, powerful drive package with field-oriented control (FOC), high efficiency, and maintenance-free components in a high-quality industrial housing. The maxon IDX drives are suitable for use across the entire speed range (from standstill to maximum speed) and have an extremely high overload capability. Together with a positioning controller, the integrated sensor (single turn) enables absolute positioning.