ALIAS Seeks to Provide Portable, Flexible Advanced Autopilot Capabilities
New program plans to leverage technological advances of the past 50 years to help reduce pilot workload, augment mission performance and improve aircraft safety
Military aircraft today have evolved over a period of decades to have ever more automated capabilities, improving mission success and safety. At the same time, these aircraft still present challenging and complex interfaces to operators, and despite demanding training regimens, operators can experience extreme workload during emergencies and other unexpected situations. Avionics and software upgrades can help, but can cost tens of millions of dollars per aircraft, which limits the rate of developing, testing and fielding new automation capabilities for those aircraft.
To help overcome these challenges, DARPA has created the Aircrew Labor In-Cockpit Automation System (ALIAS) program. ALIAS envisions a tailorable, drop‐in, removable kit that would enable the addition of high levels of automation into existing aircraft to enable operation with reduced onboard crew. The program intends to leverage the considerable advances that have been made in aircraft automation systems over the past 50 years, as well as the advances made in remotely piloted aircraft automation, to help reduce pilot workload, augment mission performance and improve aircraft safety.
"Our goal is to design and develop a full-time automated assistant that could be rapidly adapted to help operate diverse aircraft through an easy-to-use operator interface," said Daniel Patt, DARPA program manager. "These capabilities could help transform the role of pilot from a systems operator to a mission supervisor directing intermeshed, trusted, reliable systems at a high level."
As an automation system, ALIAS would execute a planned mission from takeoff to landing, even in the face of contingency events such as aircraft system failures. ALIAS system attributes, such as persistent state monitoring and rapid procedure recall, would provide a potential means to further enhance flight safety. Easy-to-use touch and voice interfaces could enable supervisor-ALIAS interaction. ALIAS would also serve as a platform for enabling additional automation or autonomy capabilities tailored for specific missions.
To familiarize potential participants with the technical objectives of ALIAS, DARPA has scheduled a Proposers' Day on Wednesday, May 14, 2014, at DARPA's offices in Arlington, Va. Advance registration is required and closes on Wednesday, May 7, 2014, at 3:00 PM Eastern Time. Participants must register through the registration website: https://www.schafertmd.com/darpa/tto/alias/. The Special Notice for ALIAS is available at http://go.usa.gov/k5zm. For more information, please email DARPA-SN-14-32@DARPA.mil.
ALIAS targets advancement in three key technical thrust areas:
(1) Minimally invasive interfaces from ALIAS to existing aircraft: It is anticipated that the ALIAS system would need to operate aircraft functions to provide automated operation. Systems generally confined to the cockpit would support the vision of portability.
(2) Knowledge acquisition on aircraft operations: To support adaptation of the ALIAS toolkit across different aircraft in a short amount of time, it is anticipated the ALIAS system would benefit from the leverage of existing host aircraft procedural information, existing flight mechanics information or models, or other methods of rapidly developing requisite aircraft information.
(3) Human-machine interfaces: A vision for ALIAS is that the human operator provides high‐level input consistent with replanning and mission‐level supervision and is not engaged in lower‐level flight maintenance tasks that demand constant vigilance.
DARPA is interested in interdisciplinary research activities that would culminate in a series of progressive systems demonstrations. These demonstrations would begin with ground-based development and demonstration of a prototype system with one aircraft type and progress to a proof-of-concept flight test involving porting the system to a different aircraft type. The program would culminate in a robust demonstration across an entire flight and responses to simulated emergency situations.
Featured Product
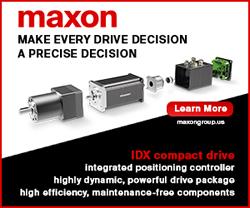