Festo Offers Faster Packaging Handling Systems with Robotics Controller
Festo provides suitable handling systems with a high dynamic response and at low cost. Festo handling systems are genuine alternatives to complex and heavy robot systems.
30 per cent faster than conventional handling units: this is the high speed T-gantry from Festo. It offers the dynamic response of a system with a linear motor at the cost of a solution with toothed belt axes - just right for the fast insertion of products into boxes. There are, however, also solutions for palletising processes - including a control cabinet and programming.
Festo handling systems are genuine alternatives to complex and heavy robot systems. Festo supplies its systems in ready-to-install form for direct integration into a plant, with all the necessary machine interfaces.
High speed T-gantry EXCT
The high-speed T-gantry can easily achieve cycle times of 670 milliseconds. It offers a higher dynamic response than conventional linear gantries and is scalable for a wide variety of strokes. It can therefore easily keep up with the cycle times of highly dynamic production processes with both present-day and future packaging machines.
The gantry has a speed of 5 m/s and achieves acceleration rates of 50 m/s² over its entire working area thanks to a clever design that connects both toothed belt axes to the cross member with a single rotating toothed belt around the drive shaft. This is driven by two servo motors type EMMS-AS or EMME-AS. A positive side effect is that there is no need to include a motor in the motion on the Y/Z plane with its two degrees of freedom.
Reduced masses and two servo motors installed in a parallel configuration allow fast and dynamic motion and result in less wear. The control package CMCA provides users with a matched application-specific and ready-to-install solution. This permits freely selectable 3D path control with highly dynamic kinematic mechanisms.
Solutions for palletising
Customer-specific systems from Festo include matched handling axes with grippers, a control cabinet and programming. Assembled from standard components such as the electric drives EGC, EGC-HD and DGEA, motors EMMS-AS or EMME-AS, a controller CMMP and a robotics controller CMXR, these solutions also include a safety system CMGA and an operator unit CDPX.
Ready-to-install handling systems, for example for palletising tasks, relieve users of virtually all the complicated working processes normally associated with the development and assembly of these systems. Users need only talk to their Festo project advisor and describe their application task. This advisor and other Festo experts will then plan, order, compile, assemble, test and deliver a complete solution directly to the user's plant, including documentation and a suitable tailor-made control cabinet. This protects all pneumatic, electrical and electronic plant components. Control cabinets are designed and built on a made-to-measure basis for a specific application - and by taking into account the needs of specific industries.
What are the advantages of handling solutions over six-axis robots? They can be easily integrated into existing control system concepts and thus in the drive technology of the entire production line. There is no need for further control systems. This reduces programming and servicing costs.
Robotics controller
Handling systems are ideal for fast transfer and positioning as well as dynamic handling in packaging processes. They are based on a Festo robotics controller CMXR. This combines mechanical components, electric drive technology and control technology to form a complete kinematic system solution and coordinates highly-dynamic motions in three dimensions. The robotics controller CMXR interpolates and positions all axes which can execute contour paths relative to a central line. The controller can set path-switching points and thus activate process devices precisely.
The CMXR is a technical virtuoso: it acts as an interface to both higher-level control systems and to the motor controllers for the servo axes and valve terminals. It also facilitates the integration of image processing systems such as the intelligent vision system SBO..-Q from Festo. The vision system can also be used together with suitable conveyor systems to realise applications with moving objects.
http://www.festo.com
Featured Product
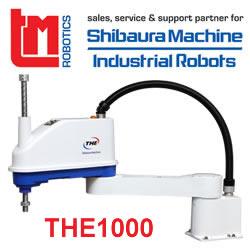
TM Robotics - Shibaura Machine THE SCARA range
The THE range from Shibaura Machine is an extensive line up of SCARA robots. Available in four arm lengths THE400 (400mm), THE600 (600mm) and the most recent THE800 (800mm) and THE1000 (1000mm), this range is suitable for assembly, handling, inspection and pick and place processes in varied industrial applications. The THE1000 boasts a 20kg payload capacity and an impressive 0.44 second cycle time, providing high speeds for processes with large components. In fact, the range has been recognised for as the price-to-performance leader compared to other SCARA models in its price range due to its impressive speed versus payload capacity.