TSE Industries to Develop Prototypes of Telescopic Hydraulic Cylinders for Advanced Telescopic Technologies, Inc. (ATT) Using TSE-EcoWind® Polyurethane Composite Resins
Canada's Advanced Telescopic Technologies, Inc. (ATT) has announced that it will begin development of its Telescopic Composite Cylinder Hydraulic Hoist products using the polyurethane composite resins of TSE Industries, Inc. of Clearwater, Florida.
Clearwater, Florida May 13, 2014
Canadian company, Advanced Telescopic Technologies, Inc. (ATT), has announced that it will begin development of its telescopic composite cylinder products using TSE-EcoWind® polyurethane composite resins manufactured by TSE Industries, Inc. of Clearwater, Florida. TSE was awarded the JEC Americas 2013 Innovation Award for its environmentally preferable TSE-EcoWind® polyurethane resin.
TSE-EcoWind® polyurethane composite resin makes filament wound pipes as strong and versatile as steel, yet lighter and less expensive. Products produced with TSE-EcoWind® Polyurethane Composite Resin are extremely resilient, long-lasting, surpass the specifications of existing resin technologies, and have superior burst strength (Pressure vessels-1250psi; Water Heaters-550psi). TSE's polyurethane resin is environmentally preferred to polyester and epoxy resins, being VOC, BPA and styrene-free, with ultra-low emissions.
"We have found the use of TSE-EcoWind® polyurethane composite resin and the unique application systems of TSE to be ideal for our cylinders, both in formulation and production," stated Larry Horne, ATT's Head of Project Development & Marketing. "We will be moving forward immediately with TSE, working with their R&D department to develop prototypes and testing of our multi-stage hydraulic cylinders."
Principals from the two companies first met at JEC Americas 2013, where both firms were presented with coveted Innovation Awards in their respective categories. The agreement between the two companies will be ratified at the JEC Americas 2014 Composite Show on May 14 in Atlanta.
"We couldn't be more excited to be selected by ATT to be its composite material provider of choice for this extraordinary product and are looking forward to working closely with them," said TSE President, Rick Klingel. "It further validates the innovative work our Composites Team has done in developing a powerful, versatile and environmentally preferable polyurethane resin."
About TSE-Industries, Inc.
TSE Industries of Clearwater, FL, provides custom molded rubber parts and extrusion, custom plastic fabrication, Millathane® millable polyurethane rubber, Thanecure® reactive additives, contract manufacturing of specialty chemicals & PUR's, TSE-EcoWind® and TSE-EcoSpray® polyurethane composite resins, as well as UHMW-PE sheet.
About Advanced Telescopic Technology Inc.
Advanced Telescopic Technologies, Inc. (ATT) offers over 30 years of experience designing, prototyping and manufacturing custom hydraulic cylinders. The company controls iron-clad patent protection for the manufacture of composite telescopic hydraulic cylinders for Canada, USA, Mexico, Europe, India, China and Hong Kong, and has Patent Cooperation Treaty (PCT) protection worldwide.
About the JEC Innovation Awards Program
Created in 1998, the JEC Innovation Awards Program is a worldwide competition that identifies, promotes, and rewards the most innovative composite solutions worldwide that create more value for end users. The selection criteria for the JEC Innovation Awards are technical excellence, market potential and originality.
Featured Product
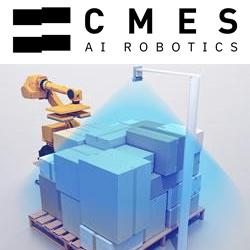
CMES - AI-Powered 3D Robot Vision
Powered by AI, CMES Robotics enables 3D vision for factory robots. CMES AI vision software enables robots to recognize unstructured, flexible, or deformed objects, pick them up, and loading and unloading. CMES Vision software has been deployed worldwide for random palletization and depalletization along with void filling applications. CMES Robotics automates your warehouse, logistics, and supply chain. For more information, please visit: cmesrobotics.com or email info@cmesrobotics.com.