Festo Offers Compact Gantry EXCM for Maximum Coverage
Turnkey planar surface gantry for compact machines The compact gantry EXCM offers maximum coverage of its working space and is ideal for applications where every millimetre counts.
The compact gantry EXCM from Festo offers maximum coverage of its working space and is ideal for applications where every millimetre counts. It combines high functionality with a compact design and an attractive price/performance ratio.
The parallel kinematic drive concept ensures low moving masses. The recirculating toothed belt guides the slide within a two-dimensional area. The fixed motors are connected to the slide. At the same time, the pre-parameterised drive and controller package simplifies commissioning.
Optimum use of space
The gantry offers an optimum ratio between required installation space and working space and is ideal for very compact machines - installed without an external control cabinet directly on a worktable. The functional drive and controller package is standard on the EXCM-10 version. It is suitable, for example, for the automation of pre- and post-analytical laboratory processes. The plain-bearing guide makes the EXCM-10 very economical.
The drive and controller package is optional on the EXCM-30 version. Its main applications are in small parts assembly and handling or in electronics manufacturing and laboratory processes. Its precise and robust recirculating ball bearing guide is able to absorb large forces and torques, even at high speed.
Featured Product
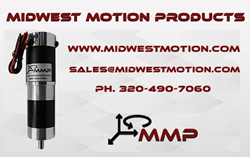
Midwest Motion Products is a leading provider of robust and reliable Motion Control Products.
MMP specializes in supplying high-quality Brushed & Brushless DC Motors & Gearmotors for Robotics and Automation Equipment with a wide range of motor windings and gear ratios. With an impressive track record of more than 8,000 released DC Gearmotors designs and over 2,000,000 individual part numbers, we are renowned for our ability to handle large-scale orders. Due to our huge on-hand inventory, we are also well known for lightning-fast delivery of our standard products. We take pride in our dedicated customer service and our team of knowledgeable sales and engineering experts who are ready to assist you with custom design solutions tailored to your specific application. Additionally, we also offer a wide range of complimentary products, such as DC Motor Controls, DC Linear Actuators, AC-DC power Supplies, and DC Servo Amplifiers and others.