New Automated Bulk Bag Filling System Streamlines Peanut Processing
The new Spiroflow Systems gain-in-weight bulk bag filling system delivers 15x productivity increase, increases weighing accuracy over 400%, reduces number of operators from nine to one and minimizes possible product contamination.
Monroe, NC July 15, 2014
Golden Grove founder Lee Swinson, a peanut farmer in Eastern North Carolina, sells his Carolina/Virginia-style peanuts to wholesalers around the world. While some peanuts are made into candy and some are roasted, packaged and sold to retailers, the majority of the 10,000 ton harvest is left raw and sold in bulk. The companys raw in-shell peanuts are packed in 900 lb bulk bags and shipped to customers around the world. As this wholesale business grew, Swinson saw opportunities to improve bulk bag filling efficiencies.
Golden Grove employees were manually filling 20 bulk bags per day. Three filling stations each contained a hopper fitted with a slide gate and a scale positioned below. An operator would open the slide gate allowing the peanuts to fall into the bulk bag until the bag was within +/- 2 lb of the target 900 lb weight. The process was extremely slow and labor intensive. Weighing accuracies could be improved to increase profitability as well.
The process also generated some spillage and possible product contamination. If the bag spout was not held firmly beneath the slide gate, peanuts fell on the floor. Operators were easily bored with the tedious process and would sometimes look at their cell phones during filling. On occasion cell phones (and other items) were dropped into the bulk bag contaminating the contents.
Golden Grove required a significantly faster contamination free process to meet the growing wholesale demand. The company turned to Spiroflow Systems who recommended an automated gain-in-weight filling system.
Golden Grove initially invested in a single Spiroflow C1-2 bulk bag filling system and the solution worked so well that they quickly purchased two more identical systems. A large elevator conveyor continually delivers peanuts to a hopper installed above each filling station. Each hopper is fitted with a 10" slide gate valve automatically operated by the filling system control panel. The C1-2 Bulk Bag Fillers installed are designed to fill customer specified 40" square bulk bags but can be adjusted to accommodate bags that are 50-64" tall with corner loops 8-10" long. All product contact parts on the bulk bag fillers are constructed from 304 Stainless Steel to meet food safety standards. A flexible connection is installed between the filling head and the base of each hopper as rigid connections would interfere with accurate weighing. A flexible connection is also installed between the bag inflation fan and the filling head. Load cells on each filler are connected to a NEMA 4 certified control panel with digital weigh batch controls, a slide gate valve position control and a bag inflation blower fan.
With the installation of three new Spiroflow gain-in-weight filling systems, the number of dedicated bulk bag filling operators was reduced from nine to one. Their filling rate increased to 300 bulk bags per day - a 15x productivity increase! Weighing accuracy increased by more than 400% and product spillage was reduced. The automated filling system eliminated all operator contact with the product which significantly reduced possible product contamination.
The new bulk bag filling system delivers the speed the company needed to meet their growing wholesale business demands. Swinson commented, "Spiroflow is always willing to work with us. Their Controls Engineer worked on-sight to program the control panels which was well worth the investment." Lee added, "Spiroflow bulk bag fillers are simple and durable. The Spiroflow solution delivered the filling speed we needed and more."
For over 40 years, Spiroflow Systems has designed, engineered and manufactured its leading line of powder handling and conveying solutions. The company offers a wide range of standard and custom options for both small and large volume users. Products include bulk bag unloaders (also called bulk bag dischargers) and bulk bag fillers, flexible screw, aero mechanical, tubular cable drag, tubular chain drag and pneumatic conveyors, box, bag and drum dump stations, robotic palletizing, and the ‘Pacepacker range of automatic packing, pick and place solutions.
Primary markets include food, snack food, confectionery, beverage, dairy, pet food, cement, chemical, plastics, ceramics, bricks, glass, minerals, water treatment, environmental, waste and recycling, pharmaceutical, and packaging. For more information about Spiroflow Systems and their complete product line of powder handling solutions visit http://www.spiroflowsystems.com or call 704-246-0900 to discuss your specific requirements.
For more information on Golden Grove visit their website at http://www.goldengrove.com.
Featured Product
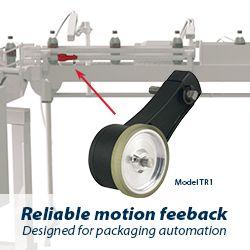
Model TR1 Tru-Trac
The Model TR1 Tru-Trac® linear measurement solution is a versatile option for tracking velocity, position, or distance over a wide variety of surfaces. An integrated encoder, measuring wheel, and spring-loaded torsion arm in one, compact unit, the Model TR1 is easy to install. The spring-loaded torsion arm offers adjustable torsion load, allowing the Model TR1 to be mounted in almost any orientation - even upside-down. The threaded shaft on the pivot axis is field reversible, providing mounting access from either side. With operating speeds up to 3000 feet per minute, a wide variety of configuration options - including multiple wheel material options - and a housing made from a durable, conductive composite material that minimizes static buildup, the Model TR1 Tru-Trac® is the ideal solution for countless applications.