IMTS 2014 - Fanuc - Series 30i CNC
FANUC's new Series 0i-F CNC is the latest generation of the world's most popular and best value Series 0i CNC that now has commonality of design to the versatile Series 30i CNC and a 15" display option.
FANUC America Corporation introduces CNC innovations that improve machining performance, ease of use and maintenance at IMTS 2014 Booth #S-8919. These include: introduction of the new Series 0i-F CNC with new commonality of design and 15" display option, a new CNC platform with built in Bluetooth technology and digital servo adapter with new EtherCAT interface.
FANUC's new Series 0i-F CNC is the latest generation of the world's most popular and best value Series 0i CNC that now has commonality of design to the versatile Series 30i CNC and a 15" display option. The Series 0i-F boasts common operability, maintainability and networking options as the Series 30i CNC along with having a highly compatible PMC ladder. This translates to easier operation and maintenance across the plant floor. The seamless combination of using the same motors, amplifiers, peripheral devices (safety machine operator's panel, I/O module/unit, iPendant, interface unit for handy machine operator's panel) as the Series 30i further simplifies the ease of use and maintenance of the Series 0i-F. Seamless and common PMC functions among both the 0i-F and 30i-B CNCs include: multi-path PMC, ladder dividing management, function block, multi-language comment and I/O Link i. With an increased axis number of 9 total controlled axes for a 1 path system for both 0i-MD (milling) and 0i-TD (turning) and a 2 path system now available on the 0i-MF with 11 total controlled axes, the Series 0i-F is more versatile to improve machining performance. Additional new features on the Series 0i-F include: 15" display, I/O Link i, FSSB high speed rigid tapping, function for loader control, tolerance control, axis name expansion, program folder management, quick program restart, flexible path axis assignment, multi-path PMC function, ladder dividing management, EtherNet/IP and PROFINET.
FANUC's new standard CNC platform allows for enhanced CNC functionality using PC technology. Built in Bluetooth on the CNC allows for the use of wireless technology that can operate a CNC by keyboard or mouse. So, via remote desktop it is possible to transfer data between a tablet and CNC. Advanced PC applications such as CAD/CAM or NCGuide are now available on the CNC remotely without leaving the machine. This improves functionality and use of the CNC. Other new features of FANUC's new standard CNC platform include: enhanced 3D graphics with MANUAL GUIDE i, new data server with larger storage and use of peripheral devices such as keyboard and mouse.
FANUC's Digital Servo Adapter with new EtherCAT interface adds more power to applications needing high-speed and high-accuracy. The Digital Servo Adapter allows for FANUC servo motors to be run from a separate controller over EtherCat. From 1 to 8 axes can be controlled, including a spindle interface and multiple large servo motors - up to 3 large servo motors at a time for industrial machines. The Digital Servo Adapter can replace hydraulic and other brand servo drives with high accuracy and high performance FANUC servo motors. The EtherCat interface is ideal for industrial machines such as: servo press machines, wire saw machines and electric injection molding machines.
Featured Product
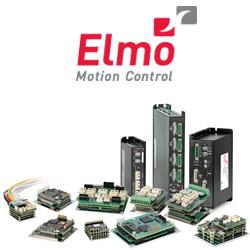