Schunk - Analog multi-positioning monitoring via teachable C-slot sensor
08-06-2014 - The analog SCHUNK MMS-A magnetic switch is the first teachable encoder which can be integrated directly into the C-slot of gripping modules free of interfering contours. It serves to accurately detect the size of the gripped parts which can be output as an analog voltage value as 0-5 V DC or 0-10 V DC, as selected, during the current handling process. Now the extremely compact MMS-A, with a 4 mm diameter, is sufficient where previously several magnetic switches were required.
The required electronics are already fully integrated. The output signal is sent over a displacement measuring range up to 30 mm with a resolution of up to 0.1 mm. Using an intuitive teaching function and two LEDs, different magnetic fields can be quickly and easily made linear. To ensure high repeat accuracy, the magnetic analog switch is specifically tailored to the relevant modules from the comprehensive SCHUNK standard program. Together with the SCHUNK FPS-F5 force sensor system controller, the encoder becomes a simple teachable multi-range sensor which can detect up to five teachable states. The MMS-A has a rugged housing for industrial use and meets protection class IP67. It can be flexibly integrated into systems via the cable outlet (30 cm, 100 cm). The operating voltage is between 15 V and 30 V.
Featured Product
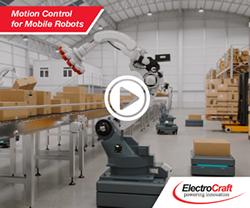
ElectroCraft's Motion Control for Mobile Robots
ElectroCraft is showcasing its award-winning mobile robot technology including their powerful and compact wheel drives, high-torque-density brushless DC motors, precision linear actuators as well as servo motor drive technology at a variety of conferences and tradeshows including the Boston Robotics Summit. Robotics Summit is the premier symposium for the sharing of ideas, technology, and market developments for robotic technologies across industries. Beyond a showcase and pitch of product, ElectroCraft is eager to participate in the collaborative discussion of challenges and opportunities that will shape the near and long-term robotic marketplace.