Flying Robots Equipped to Perform Complicated Manipulation Tasks Autonomously
There are many situations where its impossible, complicated or too time-consuming for humans to enter and carry out operations. Think of contaminated areas following a nuclear accident, or the need to erect structures such as antennae on mountain tops. These are examples of where flying robots could be used.
ROBOTS TAUGHT TO THINK AND ACT AUTONOMOUSLY
The EUs ARCAS project (Aerial Robotics Cooperative Assembly System) has designed a range of different flying robots with multi-joint manipulator arms to work together on grasping, transporting and depositing parts safely and efficiently. The autonomy and skills of the robots is being developed to build or disassemble structures for a host of future applications, from rescue missions to inspection and maintenance in the energy and space sectors.
‘The idea is that the robots should be able to fly in anywhere where it is impossible or impractical for piloted aircraft or ground robots to operate, explained ARCAS project manager Professor Aníbal Ollero, of the University of Seville. ‘We have helicopters, and multi-rotor systems with eight rotors to give more hovering control, increase the payload and carry arms with greater degrees of freedom.
Up to 10 mini-prototypes have been demonstrated working together on an indoor test bed at CATEC , the Advanced Aerospace Technologies Centre in Seville, Spain. Larger outdoor demonstrations using adapted helicopters and bigger multi-rotors have been performed at the facilities of DLR , the German national aerospace research centre, near Munich, and the University of Seville , to grasp bars and transport them over distance before depositing them.
The idea of flying robots is not new, of course. A large range of unmanned aerial vehicles are already in use, not least to take photographs and collect other sensor data. But ARCAS is pioneering in that the flying robots are being equipped with arms to perform increasingly complicated manipulation tasks autonomously. They are programmed with briefing information and 3D maps to orient them, equipped with sensors to adapt to mistakes (such as the dropping of a part) or changing circumstances (like weather conditions), and even taught how to land safely in an emergency or fly home automatically when they lose contact with base.
‘The robots work very well," said Professor Ollero. ‘We still need to improve accuracy and repetitiveness in different conditions, but the results are very promising. We have demonstrated aerial manipulation with six- and seven-joint arms and perception and planning functionalities, and this is a first worldwide. Now the aim is to improve the robots robustness and reactivity, working them together in bigger numbers and increasing the complexity of tasks they perform.
FROM PIPELINE INSPECTION TO SPACE JUNK
ARCAS is paving the way for the flying robots to be used in applications as soon as national safety laws allow. At first, this is likely to be for inspection and maintenance purposes: oil and gas pipelines and electricity networks stretching over thousands of kilometres, for example. In the medium term, the team believes the robots could cooperate in fast building of structures, such as antennae stations in remote areas or platforms between buildings, say, to rescue people from fires. In the long term, post-2020, they will be able to dismantle satellites, service space stations or even help remove space junk.
The ARCAS project (Aerial Robotics Cooperative Assembly System), involves eight partners from five countries and is funded to the tune of 6.15 million euros by the European Commissions 7th Framework Programme. It began in 2011 and finishes in November 2015.
Featured Product
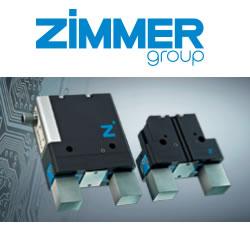
Zimmer Group - THE PREMIUM GRIPPER NOW WITH IO-LINK
IO-Link is the first standardized IO technology worldwide for communication from the control system to the lowest level of automation.