NASA Seeks Ultra-lightweight Materials to Help Enable Journey to Mars
The goal of this Game Changing Development Program effort is to develop and demonstrate scalable and cost-effective manufacturing approaches to produce ultra-lightweight core materials both as flat panels and curved structures.
WASHINGTON, Oct. 24, 2014 -- NASA is seeking proposals to develop and manufacture ultra-lightweight materials for aerospace vehicles and structures of the future. Proposals will demonstrate lower-mass alternatives to honeycomb or foam cores currently used in composite sandwich structures.
Composite sandwich structures are a special type of material made by attaching two thin skins to a lightweight core. This type of composite is used extensively within the aerospace industry and in other applications where reducing weight while maintaining structural strength is important. A common use for these sorts of composites is the shrouds for launch vehicles and other key technology components that will enable our journey to Mars.
The goal of this Game Changing Development Program effort is to develop and demonstrate scalable and cost-effective manufacturing approaches to produce ultra-lightweight core materials both as flat panels and curved structures. The final products will have half or less the area density of conventional honeycomb cores, with equal or better mechanical properties.
Over the next year, NASA's Space Technology Mission Directorate (STMD) will continue to seek industry and university partnerships to assure the agency has the capabilities it needs, while helping America maintain its leadership in the technology-driven global economy. These investments will focus on in-space propulsion and advanced high-power solar arrays; robotics and avionics for outer planetary exploration, especially high-reliability and low-mass, deep ice penetration systems; advanced materials, including large composite structures; and space observatory systems, with a focus on advanced optical coating materials.
"Technology drives exploration and ultra-lightweight materials will play a key role in our future missions," said Michael Gazarik, associate administrator for Space Technology at NASA Headquarters in Washington. "This call for proposals continues a cadence of solicitations that touch on a specific set of thrust areas needed to push human and robotic exploration farther in the solar system."
The reduced mass will lead to an increase in NASA's mission capability while decreasing mission costs and also may provide spinoffs that benefit diverse sectors of the economy and increase the nation's competitiveness.
Proposals will be accepted from U.S. organizations, including NASA centers and other government agencies, federally funded research and development centers, educational institutions, industry and nonprofit organizations. NASA expects to make two awards of up to $550,000 each for this first development phase.
The solicitation, entitled SpaceTech-REDDI-2015 NNH15ZOA001N-15GCD-C1 Ultra-lightweight Core Materials for Efficient Load-Bearing Composite Sandwich Structures Appendix, is available through the NASA Solicitation and Proposal Integrated Review and Evaluation System website by going to "Solicitations" and then "Open Solicitations" at: http://nspires.nasaprs.com/
NASA's Langley Research Center in Hampton, Virginia, manages the Game Changing Development program for STMD. For more information about STMD, the program, and crosscutting space technology areas of interest to NASA, visit: http://www.nasa.gov/spacetech
Featured Product
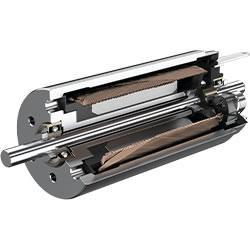
FAULHABER Drive Systems at the Robotics Summit & Expo in Boston from April 30 to May 1 in Hall C at Booth 534
Faulhaber will be presenting their drive systems for robotics and smart technology. Robots are versatile and can be found in many areas, for example, transporting goods, operating on patients or supporting the agriculture industry. With the help of robots, processes can be automated, the flow of materials optimized and employees relieved. Equipped with FAULHABER drive systems, these robots can take on tasks where the demands on function and applications are high.