Velodyne 3D LiDAR Sensor Enables M.I.T./Olin to Finish First at Maritime RobotX in Singapore; Embry-Riddle Takes Fourth
HDL-32E Sensor Guides the Way Toward Win in First-Ever Global Event
MORGAN HILL, Calif. November 05, 2014
In a spirited collaboration of men (and women) and machines, autonomous Velodyne LiDAR-equipped boats from the Massachusetts Institute of Technology/Olin College and Embry-Riddle Aeronautical University finished first and fourth at the inaugural AUVSI Maritime RobotX Challenge (http://www.robotx.org) in Singapore.
The competition, held October 20-26 at The Float in Singapores Marina Bay, was jointly organized by the National University of Singapore Faculty of Engineering, Science Center Singapore, and the Association for Unmanned Vehicle Systems International Foundation (AUVSI).
Outfitted with Velodynes HDL-32E 3D LiDAR sensor (http://www.velodynelidar.com), the pilot-less M.I.T./Olin vessel from Team Athena-Nike crossed the finish line ahead of the 14 other teams participating in the event. Team Athena-Nike, a joint partnership between M.I.T. and Olin College, came in first place overall, second place in land-based judging, and first place in the best paper category. Team Minion, from Embry-Riddle, finished fourth, after having captured first place overall at the 7th Annual International RoboBoat Competition held July 13 in Virginia Beach, Virginia.
Students from 15 universities representing five countries - Singapore, Australia, Japan, South Korea and the U.S - participated in the competition. All teams were required to outfit an unmanned surface vehicle with sensors, computers, and software, and guide the vehicle to complete a course based on various maritime missions. On the course, each team's vessel had to complete a set of tasks, including the avoidance and detection of obstacles, identifying and reporting on a specified target, and searching underwater for an acoustic source.
"The Velodyne sensor was amazing," said Michael R. Benjamin, Ph.D., M.I.T. Department of Mechanical Engineering, Computer Science and AI Lab. "I don't think we could have won this without the support from Velodyne."
"Were honored to acknowledge Velodyne LiDARs gracious contribution of the HDL-32E sensor that helped with our fourth place overall finish," said Hitesh V. Patel, Research Associate at Embry-Riddle. "The HDL-32E sensor is impressive system that has proven to be extremely rugged and reliable through several hundred hours of testing in the harsh maritime environments. Its small packaging, dense scanning and reliable readings made it an ideal choice for our RobotX Maritime platform. As a result of the reliable data, Team Minion was one of the only teams to consistently navigate the obstacle course and set the record for speed through the entry/exit gates."
"Were proud to have been a part of these two remarkable teams," said Wolfgang Juchmann, Director of Sales & Marketing, Velodyne LiDAR division. "Both M.I.T./Olin and Embry-Riddle were outstanding to work with, and we heartily congratulate both. The RobotX Challenge proved to be a very difficult set of races, drawing 15 talented teams from some of the worlds finest engineering institutions.
"Our 3D LiDAR sensors guide autonomous vehicles on land, on the seas and in the air," Juchmann said. "Were recognized worldwide for developing real-time LiDAR sensors for all kinds of autonomous applications, including 3D mapping and surveillance. And were also specialists in marine technology. For RobotX, every team used a semi self-stabilizing boat. Through our Velodyne Marine division, company CEO David Hall is building a fully self-stabilizing boat, the latest iteration of which will be demonstrated during 2015."
Velodyne Marines current vessel -- "Martini 1.5" - is a 37-foot, powered catamaran so dubbed for its ability to keep the contents of a martini in its glass, even at speeds of up to 30 miles per hour and swells approaching six feet. Martini 1.5 demonstrates a scalable, stable system that can be designed into any recreational, commercial or military vessel, thus paving the way to safer and more comfortable nautical travel in rough waters.
About Velodyne LiDAR
Founded in 1983 and based in Californias Silicon Valley, Velodyne Acoustics, Inc. is a diversified technology company known worldwide for its high-performance audio equipment and real-time LiDAR sensors. The companys LiDAR division evolved after founder and inventor David Hall competed in the 2004-05 DARPA Grand Challenge using stereovision technology. Based on his experience during this challenge, Hall recognized the limitations of stereovision and developed the HDL64 high-resolution LiDAR sensor. More recently, Velodyne has released its compact, lightweight HDL 32E sensor, available for many applications including UAVs, and the new VLP-16 LiDAR Puck, a 16-channel real-time LiDAR sensor that is both substantially smaller and dramatically less expensive than previous generation sensors. Since 2007, VelodynesLiDAR division has emerged as a leading developer, manufacturer and supplier of real-time LiDAR sensor technology used in a variety of commercial applications including autonomous vehicles, vehicle safety systems, 3D mobile mapping, 3D aerial mapping and security. For more information, visit http://www.velodynelidar.com.
Featured Product
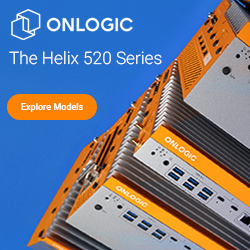
OnLogic's Helix 520 Series of Scalable Fanless Computers
The Helix 520 series utilizes the latest Intel Core Ultra processors with integrated edge AI capabilities to deliver exceptional performance and industrial-grade reliability for demanding applications in automation, robotics, machine vision, and more. Its unique modular design allows for flexible scaling of CPU and GPU performance, while robust connectivity and expansion options ensure seamless integration.