Panasonic's Industrial Robots Enhance Production Quality - CIIF2014
Panasonic is providing a wide range of new technologies and capabilities to customers in China.
SHANGHAI--Panasonic showcases its industrial solutions at the Robotics Show of the 16th China International Industry Fair held at the Shanghai New International Expo Center during November 4 - 8, 2014. In China, the manufacturing hub for many global electronics manufacturers, efforts are underway to bring network connectivity to manufacturing processes to enable stable production and to improve product quality. To assist with these efforts, Panasonic is providing a wide range of new technologies and capabilities to customers in China.
Exhibition Highlights
Three business divisions - motion control, welding systems, and motors - are taking part in this year's exhibition. Panasonic is introducing individual devices and system solutions, as well as factory automation solutions with case examples of robots at work.
Motion Control Devices
Panasonic uses Japanese technology and management expertise for locally relevant product planning and manufacturing. Panasonic has packaged into a single solution three of our globally leading technologies, which are sensors, PLCs, and laser markers.
Welding Systems
For the automotive industry, we are recommending Panasonic's "Active TAWERS" robot. When in use, there are less sparks, it can be used with different thickness of galvanized steel, and there is less distortion. These technologies have helped solve many of the issues the industry had faced.
Motors
The servo motor MINAS-A5 II N series is equipped with two-degree-of-freedom control and RTEX enabling high-speed network communication of 100Mbps. This helps improve synchronism with robots, enables smoother movement, and enhances productivity.
Currently many people in China are considering implementation of robots to cut production costs. Panasonic will use its unique technologies and know-how to improve production quality for the world.
Featured Product
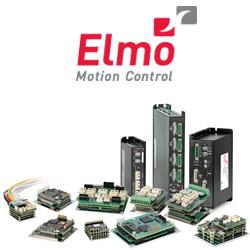