Fabtech - Metcam Sends 100 Employees to FABTECH This Week and Presents Educational Session on Reducing Environmental Footprint
Leading Fabricator Boasts the Largest Corporate Delegation at Principal Metal Industry Event in North America
November 12, 2014
Today Metcam, a fabricator of sheet metal components and assemblies for OEMs, is sending 100 employees to FABTECH, North Americas largest metal forming, fabricating, welding and finishing event, held at the Georgia World Congress Center, November 11-14, 2014. Metcam holds the distinction of having the most registrants from a single company at the event. The company has chartered two buses to transport their team to FABTECH where they will be able to observe live equipment demonstrations, network with industry peers, and discover cost-saving solutions for their business. FABTECH is anticipating 27,000 attendees with 1,400 exhibiting companies. Metcam employees will choose from over 100 educational sessions on the latest industry trends and technology.
"We are thrilled that FABTECH is in Atlanta this year and view it as a perfect opportunity to further develop our world-class Metcam team," said Bruce Hagenau, President of Metcam. "Our employees can absorb all of the knowledge, networking, and best practices that are offered through demonstrations, casual conversations, and educational sessions."
Metcam Environmental Health and Safety Manager, Sue Max will be presenting an educational session at FABTECH titled, "Reducing Your Environmental Footprint," in partnership with Kelly McCabe of Pretreatment Equipment Manufacturing, Inc., and Joseph R. Smith of Houghton International, Inc. Metcam is dedicated to being a steward of the environment and sustainable manufacturing. As such, their session will focus on implementing a sustainability program including how to overcome barriers and obstacles, setting objectives and targets, and tips for success. Metcam will discuss their initiatives such as implementing energy efficient lighting, roof replacement, and an HVAC upgrade and how they impacted the companys footprint. McCabe will talk about a new paint line installation completed at Metcam last year, and how to design a wash system that has a reduced environmental footprint and Smith will discuss how selecting the right cleaning agents can make the wash process more effective and environmentally friendly.
"We are honored to be selected to present at FABTECH as leaders in our field," said Max. "Metcam takes pride in sharing our knowledge and best practices with our colleagues in the hopes of helping others reduce their impact on the environment."
"Reducing Your Environmental Footprint" will be presented on Tuesday, November 11, 2014, at 8:00 AM.
About Metcam
Metcam is a fabricator of precision sheet metal components and assemblies for original equipment manufacturers (OEMs) representing a wide variety of industries including telecommunications, electronics and HVAC. Metcams advanced metalworking capabilities include laser cutting, punching, forming, hardware insertion, welding (including robotics), powder painting, silkscreen and parts assembly. Metcam also assists clients with product design and manufacturability to reduce their total cost of production. Metcams award-winning service, combined with an aggressive focus on quality, environmental management and lean manufacturing, simplifies the outsourcing decision for firms worldwide.
For more information, visit http://www.metcam.com.
Featured Product
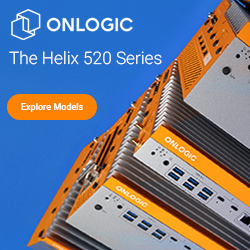
OnLogic's Helix 520 Series of Scalable Fanless Computers
The Helix 520 series utilizes the latest Intel Core Ultra processors with integrated edge AI capabilities to deliver exceptional performance and industrial-grade reliability for demanding applications in automation, robotics, machine vision, and more. Its unique modular design allows for flexible scaling of CPU and GPU performance, while robust connectivity and expansion options ensure seamless integration.