DARPA-Funded Inflatable Robotics Helps Spark Idea for Silver Screen Star
Make-believe soft robot in Disneys newest movie has roots in real-world robotics research
The giant, balloon-like inflatable robot named Baymax in Disneys Big Hero 6 has its roots in real-world research conducted by iRobot Corporation, Carnegie Mellon University and Otherlab under DARPAs Maximum Mobility Manipulation (M3) program. The films co-director, Don Hall, has said he was inspired to cast Baymax as an air-filled, soft robot after he saw an inflatable robotic arm on a visit to Carnegie Mellons Robotics Institute. Carnegie Mellons work in soft robotics has been supported by DARPA and the National Science Foundation.
DARPAs M3 program is creating and demonstrating novel design tools, fabrication methods and control algorithms to make robots more mobile and better able to manipulate objects in their environment. One area of M3 research is fabric-skinned robots that are filled with and manipulated by air.
"The M3 program has made great strides in making robots move more naturally like animals or humans move," said Gill Pratt, DARPA program manager. "Inflatable robots, like the arm developed at Carnegie Mellon, offer unique benefits such as high strength to weight, small size when uninflated, low fabrication cost, and safety when working around human beings."
This video by DARPA performer Otherlab shows the human-like motion and dexterity achievable with inflatable robotics: http://ow.ly/DZpz1
The M3 program also has developed robots that draw inspiration from four-legged animals, such as the cheetah. View the electric cheetah-bot developed by DARPA performer MIT here: http://ow.ly/DPpo2
Featured Product
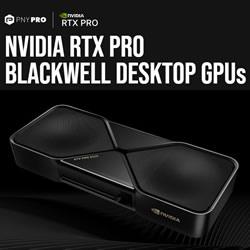