InventAIRy Project to Automatically Localize and Record Existing Inventories using Flying Robots
Standing on top of a ladder several meters high, pad and pen in hand, just to count boxes? Inventories in large warehouses could soon appear quite different and proceed to take flight, in the truest sense of those words: The goal of the InventAIRy Project is to automatically localize and record existing inventories with the aid of flying robots.
"Dear customers: the store is closed today for our regularly scheduled inventory work." Anyone who has ever encountered this or a similarly worded sign knows that "patience is a virtue" especially while shopping, while in the background, an army of employees mill about, preoccupied with numbers. The manual inspection of a goods warehouse is a fundamental component of the legally proscribed annual inventory. The conventional procedure is time-consuming and paralyzes a majority of the warehouse operations. Even the barcodes and RFID tags pervasively used today are of little help. The entire process still demands a vast amount of personnel and time.
Marco Freund is keenly familiar with the problems that must be confronted when running an inventory. The certified logistics specialist heads the InventAIRy Project at Fraunhofer Institute for Material Flow and Logistics IML in Dortmund. His vision of an optimized inventory system looks like this: "The person in charge is sitting at his desk and at the press of a button, can inspect inventories or perhaps search for a specific item - without incurring any staffing or logistics costs." To ensure this becomes reality in the not-too-distant future, Freund and his colleagues engineered a "dynamically animated records system" that distinguishes itself - on one rather critical point - from commonly available solutions currently in use today: "Goods and pallets can already be tracked automatically, via RFID for instance. In doing so, the antennas that the chips read out are permanently mounted to the shelf. The chips are located on the products and are recorded if they pass the readout device. With InventAIRy, exactly the opposite applies: The radio chips remain in their fixed position, the antenna is moved by its integration into a flying robot. "The Inventory Assistants, which the scientists have in mind, are autonomous robots that move throughout the warehouses by flying.
Putting wings to flying assistants
It is already a reality with driverless transportation systems, so it should also be possible to put them to flight with InventAIRy: In this project, the IML researchers are moving toward the goal of engineering autonomous flying robots that are capable of independently navigating and conducting inventory. These flying assistants should be able to localize objects both in the warehouses as well as the exterior area, and be able to track through barcodes and RFID tags. The advantage: These robots act independent of ground-based obstructions. Furthermore, they can move in any direction and see into hard-to-reach places, such as tall storage shelves.
The individual service robot, as an intelligent mobile object, perceives its environment dynamically on two levels: It detects how the warehouse is configured using motion and camera sensors, for instance, and can orient itself within the warehouse. GPS determines its position outside. In addition, the robot records the stored items in terms of content. The scientists accomplish this with the aid of optical sensors or radio sensors. "We take a look at various key problem sets at the same time: robustly designed, lightweight flying robots that can reliably recognize their surroundings, as well as intelligent software for their route planning and coordination," the certified logistician explains. "To ensure this solution is also appealing to small- and medium-sized enterprises, we intentionally dispensed with the installation of an expensive local infrastructure that the robots can use to orient themselves. The researchers want to accomplish this with the aid of intelligent algorithms. The flying objects should prepare maps of the warehouse on a fully automated basis, and independently modify them if there are any changes. The basis for this are, for example, ultrasound sensors, 3D cameras, and laser scanners.
Current solutions are able to integrate collected inventory data automatically into existing warehouse administration systems, without requiring additional software development. InventAIRy researchers, by contrast, are working on smart interfaces that transmit data wirelessly into existing systems. This means commercial operations save time and money - and documentation errors decrease. Furthermore, the flying robots can continuously monitor warehouse inventories. "In this manner, it would be possible to identify materials bottlenecks at an early stage in production, and rectify them even before the shortfalls can occur," adds project manager Freund. The teams preliminary results are highly promising. "By mid-2015, we intend to start with a partially automated flight. In this phase, the robot equipped with the identification technology hovers - without having to be controlled via remote operation - at one position, and circumvents collisions with obstructions, such as shelves," the project manager explains.
http://www.fraunhofer.de/
Featured Product
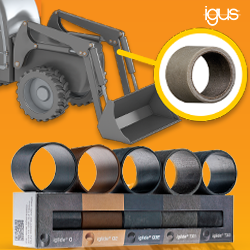