Effective, Automated Cleaning of 3D and SL Printed Parts with Graymills Help
Remove uncured SL material and residue from printed pieces quickly and thoroughly with a parts washer, rather than time-consuming hand cleaning. Let Graymills develop the system that will enhance your efficiency and improve product output.
With Graymills, you partner with a company that understands cleaning technology and can work with you to ensure that your printed part is properly handled and cleaned. Cleaning action, bath temperature, chemistry compatibility, and cleaning action are the topics of discussion with Graymills' experts when you work with them to develop a cleaning system that will minimize the drudgery and man hours from your production.
Graymills has the widest range of cleaning methodologies of any parts washer manufacturer backed by a 75 year history of design, manufacturing quality and service. They offer cleaning options from small single cell units that easily integrate into a lab or R&D setting, up to fully modular units that can move parts through multiple stages such as rinse, wash, coat and dry.
With their Total Cleaning Perspective, Graymills can steer you to the equipment that is truly best for your application. Along with on-site engineers that enhance existing designs to fit specific applications, Graymills runs a testing lab for complementary cleaning tests to eliminate the risk of purchasing a system that won't work. You can try before you buy.
Located and manufactured in Chicago, Illinois, Graymills products are supported by a nationwide network of representatives who understand cleaning and stand behind their products. Contact Graymills to discuss your 3D Printing and/or Stereo Lithography parts cleaning needs. Graymills Corporation, 3705 N Lincoln Ave, Chicago, IL 60613, www.graymills.com, sales@graymills.com, 773-248-6825.
Featured Product
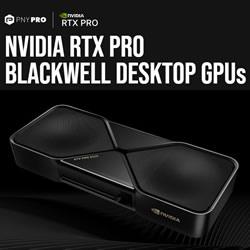